Nächster Artikel
Produktion
Zukunftsweisende Automatisierung am Fraunhofer IKS
Die Erweiterung von etablierten Automatisierungssystemen für neuartige Anwendungen soll den Weg ebnen zur Automatisierung der Zukunft. Das Fraunhofer IKS erforscht, wie der Wandel dorthin im Einzelnen aussieht. Welche Rolle Prototypen dabei spielen und welche Erkenntnisse sie liefern, lesen Sie in diesem Beitrag.
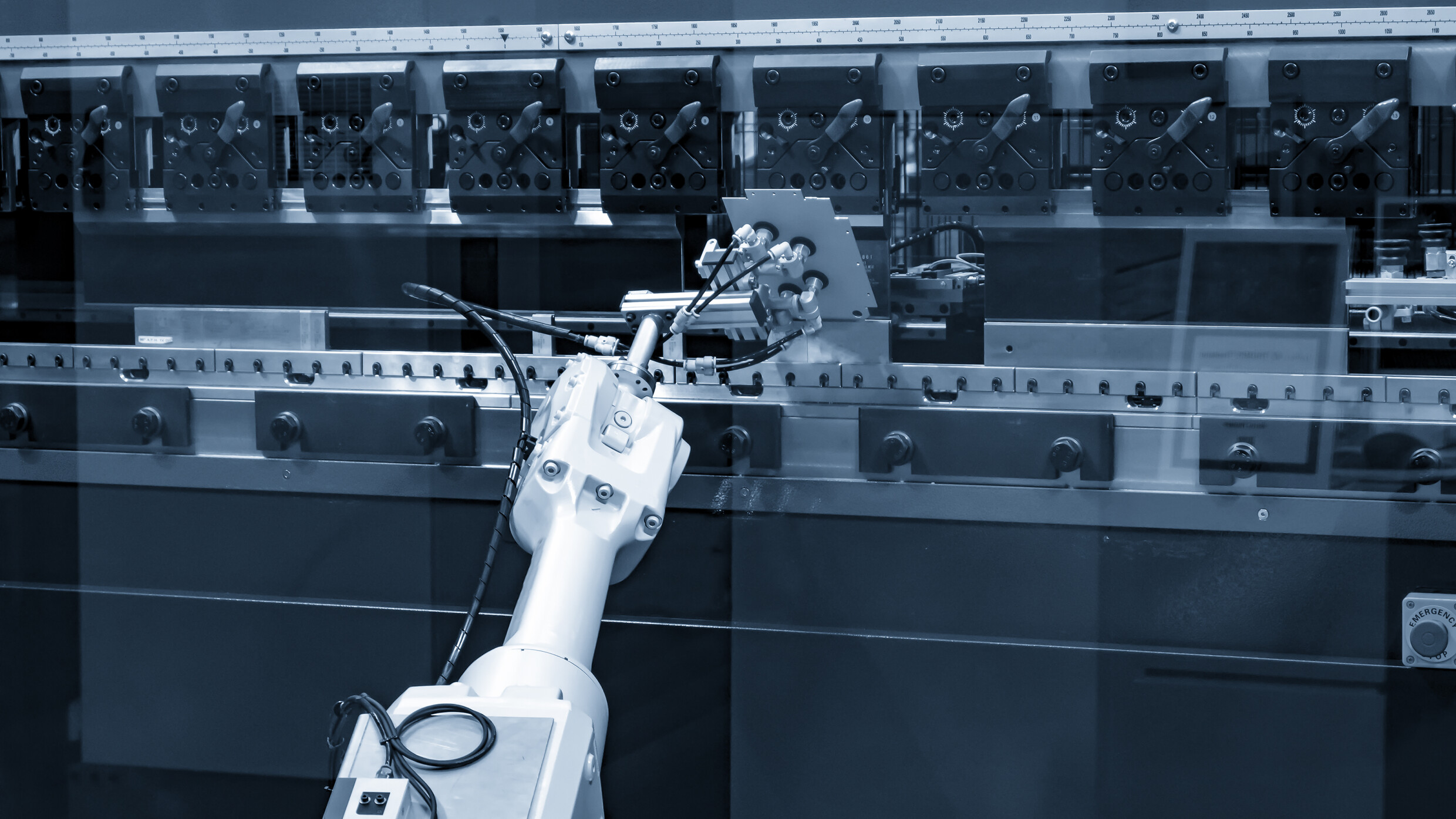
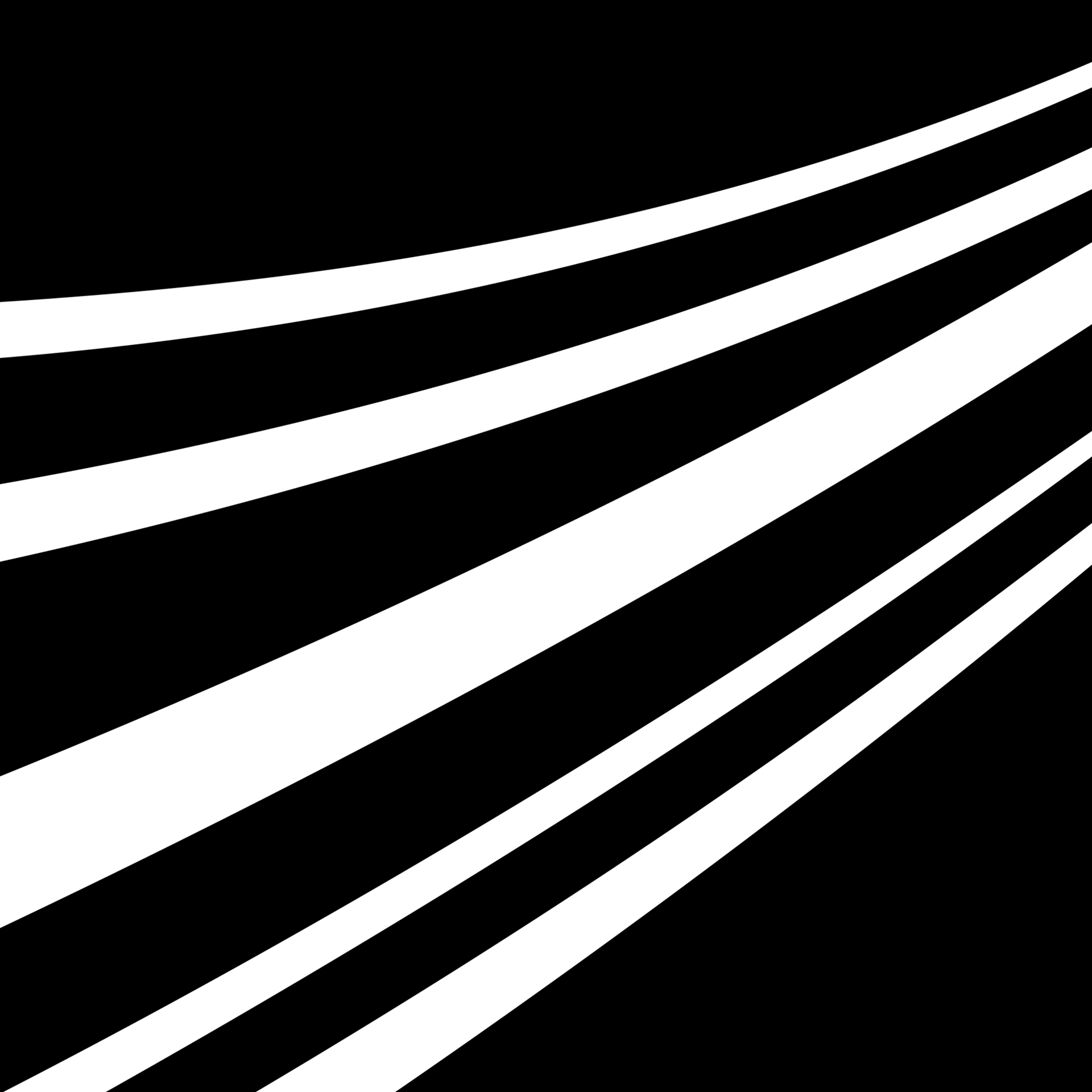
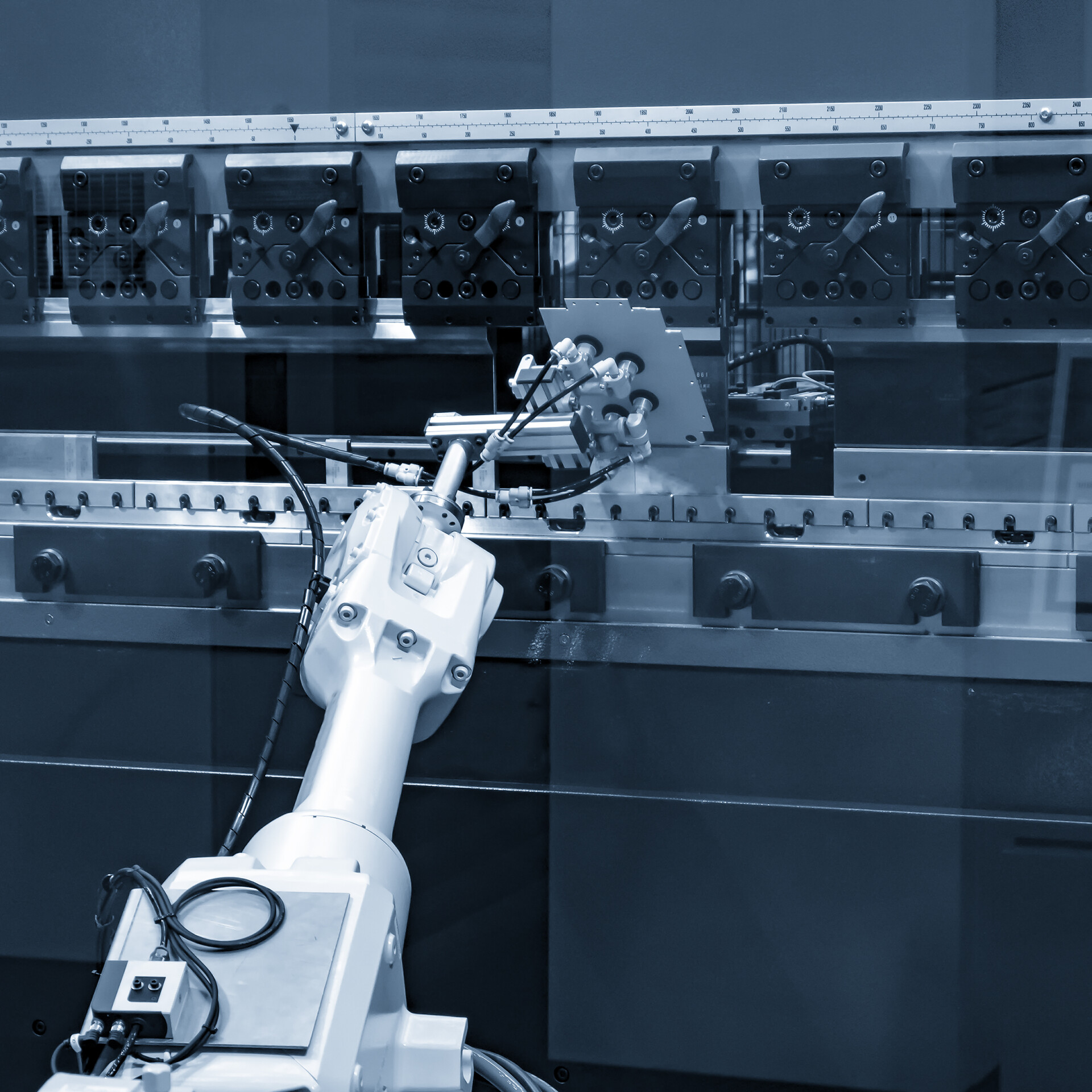
© iStock/Phuchit
Das Bestreben der Fertigungsunternehmen, wettbewerbsfähig zu bleiben, treibt die Nachfrage nach neuen industriellen Automatisierungslösungen voran. Insbesondere besteht ein wachsendes Interesse an Ansätzen, die den Grad der Flexibilität innerhalb der Produktionslinie erhöhen und die Herstellung hochgradig kundenspezifischer Produkte in kleinen Chargen ermöglichen. Gleichzeitig benötigen Unternehmen Maschinen mit verbesserten Fähigkeiten zur sicheren und effizienten Zusammenarbeit mit den Arbeitskräften in der Fertigung: Ziel dabei ist es, die menschlichen Fähigkeiten zu nutzen und auch in Zeiten des Fachkräftemangels eine hohe Qualität zu gewährleisten. Um zu erforschen, wie sich diese Anforderungen in der Praxis umsetzen lassen, haben Wissenschaftlerinnen und Wissenschaftler des Fraunhofer-Instituts für Kognitive Systeme zwei Demo-Systeme gebaut, die den Stand der Technik in der Fertigung vorantreiben.
Flexible Produktion
Das erste praktische Szenario wurde als Beispiel für eine Losgröße-1-Produktion gewählt, bei der ein hohes Maß an Variabilität und Flexibilität bei der Herstellung erforderlich ist. Es handelt sich um eine modulare Verschlussfabrik (vgl. Abbildung 1), in der abstrakte Produkte, bestehend aus einem Magazin, einem oder mehreren Ringen und einem Verschluss, montiert werden. Für jeden Montageschritt ist eine unabhängige Produktionsstation mit den erforderlichen Werkzeugen zuständig, und das teilmontierte Produkt wird von einem autonomen mobilen Roboter (AMR) von einer Station zur nächsten transportiert. Dieser modulare Aufbau erhöht die Möglichkeit der kundenspezifischen Anpassung (z. B. Zusammenbau eines Produkts ohne Ring oder Kappe oder Änderung der Farbe dieser Komponenten) und ermöglicht den parallelen Einsatz verschiedener Stationen; das heißt die gleichzeitige Bearbeitung mehrerer Aufträge.
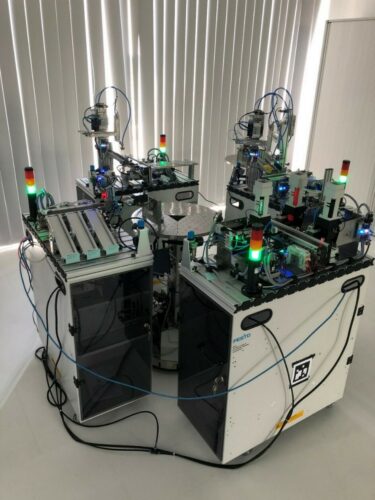
Abbildung 1: Überblick über die Kappenfabrik, in der unabhängige Stationen mit Hilfe eines autonomen mobilen Roboters flexibel ein Produkt zusammensetzen.
In diesem Zusammenhang wird ein Rahmenwerk eingesetzt, das den Einsatz von KI-Techniken in der Produktion unterstützt und die folgenden Techniken umfasst:
- Digitale Zwillinge: Die Überwachung und Dokumentation des Zustands jeder Produktionsstation, einschließlich der aktuellen Verfügbarkeit von Komponenten für die Montage, erfordert maschinenlesbare Datenblätter der Stationen – sogenannte digitale Zwillinge. Diese Modelle werden mit Hilfe von Asset Administration Shells strukturiert, einem sich schnell entwickelnden Darstellungsstandard in der Automatisierungsdomäne.
- Vertragsbasierte Bereitstellung: Das Framework stützt sich auf eine serviceorientierte Architektur, um sicherzustellen, dass seine Module – die als Services verpackt sind – flexibel eingesetzt werden können. Jeder Service hat einen zugehörigen Service Contract, in dem die Daten- und Ressourcenanforderungen des Services dokumentiert sind. Anhand dieser formalisierten Contracts kann vor der Bereitstellung geprüft werden, ob der gewünschte Host die Anforderungen für die erfolgreiche Ausführung der Dienste erfüllen kann. Dieser Mechanismus ist auch nützlich, wenn Dienste dynamisch neu bereitgestellt werden müssen, falls ein Host plötzlich nicht mehr verfügbar ist.
- KI-basierte Analyse: Das Framework vereinfacht den Einsatz von KI zur Durchführung verschiedener Aufgaben in der Produktion. So kann beispielsweise die visuelle Qualitätsanalyse von Produkten durch das Trainieren und Bereitstellen eines maschinellen Lernmodells anhand von Bildern, die von Kameras in der Fertigung aufgenommen wurden, durchgeführt werden. Neben der visuellen Qualitätsprüfung gibt es natürlich noch viele andere Anwendungsfälle in der Fertigung, die vom Einsatz von KI profitieren, darunter die vorausschauende Wartung, die Bestandsoptimierung usw.
- Automatisierte Modellumschulung: Mit der Zeit können KI-Modelle, die zur Analyse eingesetzt werden, ungenau werden. Wenn beispielsweise ein Modell für die Qualitätskontrolle verwendet wird, können irgendwann neue Produktanpassungen eingeführt werden, für die das Modell nicht trainiert wurde, was zu unzuverlässigen Analyseergebnissen führen würde. Um dies zu vermeiden, kann das Framework automatisch erkennen, wenn die Perfomance eines Modells gering ist, und ein erneutes Training mit neueren Daten auslösen.
Zur Unterstützung des Frameworks wurde ein Dashboard (vgl. Abbildung 2) eingesetzt, das in Echtzeit Einblicke in den Zustand von Services, Geräten und Prozessen in der Produktionslinie gibt und die Analyseschritte für eingesetzte KI-Modelle überblickt. Dies ermöglicht es den Produktionsleitungen auch, von einer zentralen Stelle aus schnell auf Änderungen zu reagieren.
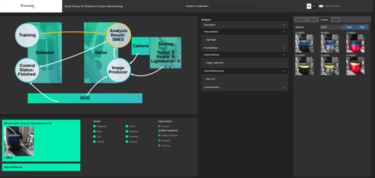
Abbildung 2: Dashboard für das Framework, das den Zustand der Produktionslinie und des Services sowie Informationen über aktive KI-Modelle anzeigt.
Mensch-Maschine-Interaktion
Das zweite Szenario wurde als Beispiel für eine auf den Menschen ausgerichtete Produktion gewählt, bei der das Ziel nicht darin besteht, menschliche Arbeitskräfte zu ersetzen, sondern sie bei wichtigen Fertigungsschritten in einem neuen Produktionsparadigma zu unterstützen. Es geht um die Zusammenarbeit zwischen einem menschlichen Arbeitenden und einem Roboter – genauer gesagt, einem leichten Roboterarm – in der Werkstatt (siehe Abbildung 3). Das Design dieser so genannten Cobots ermöglicht es Menschen und Robotern, sich denselben Arbeitsbereich zu teilen.
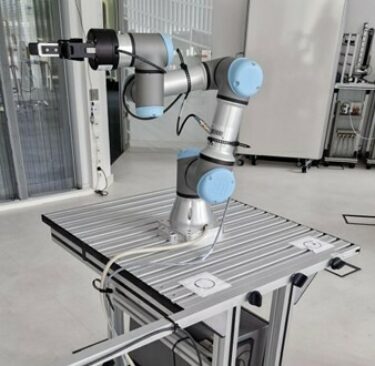
Abbildung 3: Leichtgewichtiger Roboter für die Zusammenarbeit zwischen Mensch und Maschine in der Fertigung.
In dem Szenario erledigt der Arm selbstständig eine Aufgabe der Maschinenbeschickung, während in anderen Phasen menschliche Arbeitskräfte benötigt werden. Das bedeutet, dass Roboter und Mensch den Raum in der Werkstatt aushandeln müssen, und es sind Sicherheitsmaßnahmen – Begrenzung der Höchstgeschwindigkeit des Roboters und Auslösen sicherer Stopps – erforderlich, um Verletzungen durch Kollisionen und Einklemmunfälle zu vermeiden. Gleichzeitig dürfen diese Sicherheitsmaßnahmen aber nicht ständig ausgelöst werden, damit vernünftige Taktzeiten und Durchsatzleistungen erreicht werden können. Um dieses adaptive Verhalten zu realisieren, wurde mit Hilfe des Model-based safety engineering und einiger wichtiger Forschungsergebnisse ein modulares Sicherheitskonzept entwickelt:
Kontakt
Sie haben noch Fragen oder möchten noch mehr zum Thema erfahren? Dann wenden Sie sich bitte sich an unseren Experten Alexandre Sawczuk da Silva.
- Modellbasierte Sicherheitstechnik: Die Systemsicherheit wird anhand eines Zuverlässigkeitsnachweises argumentiert, was in vielen sicherheitskritischen Bereichen wie der Automobil-, Eisenbahn- oder Luftfahrtindustrie gängige Praxis ist. Der Zuverlässigkeitsnachweis wird unter Bezugnahme auf ein formalisiertes Modell der zulässigen Umgebung des Systems erstellt - die sogenannte Operational Design Domain (ODD).
- Sicherheitsgarantie für die Erkennung: Die Reaktivität des Systems wird teilweise durch eine KI-basierte Wahrnehmung erreicht, die umfangreiche Informationen wie den Standort von Menschen und Klassifizierungen je nach ihrer Rolle (d. h. trainiert oder nicht trainiert) ausgibt. Eine klar definierte ODD unterstützt das Argument für den Einsatz von KI-Funktionen in einer sicherheitskritischen Anwendung.
- Modelle des menschlichen Verhaltens: Der Sicherungsfall beruht auf Annahmen über das Verhalten der menschlichen Arbeiter, wenn sie sich in der Nähe des Roboters befinden. Die explizite Modellierung dieser Annahmen sowie der zu erwartenden Abweichungen vom "korrekten" Verhalten der Arbeitskräfte ermöglicht es, auch adaptiv auf das Verhalten der Menschen zu reagieren.
- Umschaltung des Sicherheitskonzepts: Alle diese Modelle zusammen ermöglichen die Umschaltung zwischen verschiedenen Betriebsarten während der Laufzeit: Anhand der beobachteten Daten über den Menschen und die Umgebung ermittelt das System das jeweils gültige Sicherheitskonzept und leitet daraus die entsprechende Betriebsart ab.
Es wurde ein Simulator entwickelt, um diese Einrichtung in Aktion zu zeigen. Der Roboter kümmert sich um eine Maschine, während der Arbeitsbereich für menschliche Arbeitende überwacht wird. Wenn Menschen mit unterschiedlichen Rollen und Verhaltensweisen den Arbeitsbereich des Roboters betreten, ändert sich seine Arbeitsweise entsprechend.
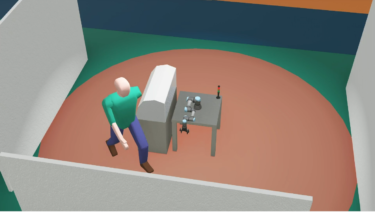
Abbildung 4: Screenshot der Simulation, in der sich ein ungeschulter Arbeiter dem Roboterarm nähert. In diesem Fall wird ein sicherer Stopp ausgelöst.
Wie in Abbildung 4 dargestellt, wird bei Annäherung eines ungeschulten Arbeiters (in grüner Kleidung) an den Roboter ein sicherer Stopp ausgelöst, um Kollisionen und Unfälle durch Einklemmen zu vermeiden. Der Sicherheitsabstand (roter Kreis auf dem Boden) wird mithilfe eines physikalischen Modells berechnet, das sicherstellt, dass dieser Abstand ausreicht, um den Roboter rechtzeitig zu stoppen, bevor es zu einer Kollision kommen kann.
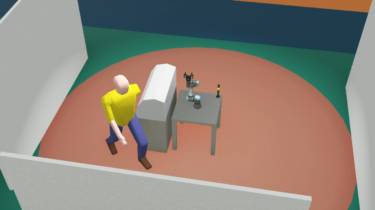
Abbildung 5: Screenshot der Simulation, bei der sich ein geschulter Arbeiter dem Roboterarm nähert. In diesem Fall arbeitet der Roboter weiter, allerdings mit einer begrenzten Höchstgeschwindigkeit.
Bei geschulten Arbeitern, wie der in Abbildung 5 gezeigten Person (in Gelb), muss ein sicherer Stopp nicht ausgelöst werden, da davon ausgegangen wird, dass der Mensch weiß, wie er sich in der Nähe des Roboters zu verhalten hat. Die Begrenzung der Höchstgeschwindigkeit ist daher ausreichend, um die Sicherheit zu gewährleisten.

Abbildung 6: Screenshot der Simulation, bei der sich ein geschulter Arbeiter dem Roboterarm mit hoher Geschwindigkeit nähert. In diesem Fall wird ein sicherer Stopp für den inneren Sicherheitsabstand ausgelöst.
Wenn jedoch ein anderer geschulter Arbeiter (Abbildung 6, orangefarben) gegen diese Annahme verstößt, indem er sich zu schnell bewegt, schaltet der Roboter in einen dritten Betriebsmodus. In diesem Fall bewegt sich der Roboter mit einer begrenzten Höchstgeschwindigkeit innerhalb des Sicherheitsabstands. Nähert sich der Arbeiter dem Roboter dann näher als ein zweiter Sicherheitsabstand (gelber Kreis), wird ein sicherer Stopp ausgelöst.
Dieser Demonstrator zeigt unsere Vision von einer rationalisierten Zukunft der Fertigung mit einer sicheren und effizienten Mensch-Maschine-Kollaboration. Die Sicherheit bildet die Randbedingungen, unter denen die Produktivität des Fertigungsprozesses optimiert wird. Der Roboter führt nur diejenigen Sicherheitsmaßnahmen durch, die für das Szenario unbedingt erforderlich sind und bietet ansonsten maximalen Nutzen.
In der Zukunft
An den beiden oben vorgestellten Szenarien wird aktiv gearbeitet, und es ist geplant, ihren Anwendungsbereich weiter auszubauen. So kann beispielsweise der gleichzeitige Einsatz mehrerer AMRs im Szenario der flexiblen Produktion untersucht werden, indem die Ideen der parallelisierten Auftragsplanung und des Flottenmanagements in das bestehende System integriert werden. Ebenso lässt sich das Szenario der Mensch-Maschine-Interaktion erweitern, um eine engere Zusammenarbeit zwischen Menschen und Robotern zu untersuchen, bei der die Maschine den Arbeitenden direkt bei seiner Aufgabe unterstützt. Schließlich ist es möglich, beide Szenarien zusammenzuführen, um die Herausforderungen einer sehr komplexen Fertigungshalle zu bewältigen.
Viele der hier erörterten Ideen, die dem neuesten Stand der Technik entsprechen, lassen sich erfolgreich in die Industrie übertragen und für den Betrieb in großen Industrieumgebungen aufstocken. Um dies zu erreichen, kann das Fraunhofer IKS bei der Migration zu neuen Konzepten helfen, von der schrittweisen Erweiterung bestehender Systeme bis hin zur Unterstützung bei der Einführung und Bewertung völlig neuer Anwendungsfälle. Wenn Sie Fragen dazu haben, wie Sie diese Techniken für Ihr Unternehmen nutzbringend einsetzen können, zögern Sie bitte nicht, uns zu kontaktieren. Unsere Experten beraten Sie gerne, wie Sie diese innovativen Ansätze zur Optimierung Ihres Unternehmens am besten einsetzen.
Diese Arbeit wird vom Bayerischen Ministerium für Wirtschaft, Landesentwicklung und Energie im Rahmen eines Projekts zur Unterstützung der thematischen Entwicklung des Instituts für Kognitive Systeme IKS finanziert.