Nächster Artikel
Zukunft der Produktion
Auf dem Weg zu Industrie 5.0?
Die industrielle Produktion befindet sich in einem radikalen Umbruch. Mit den fortschreitenden technologischen Möglichkeiten und dem gesellschaftlichen Wandel muss sich auch die Industrieautomatisierung neu erfinden, um sich geänderten Anforderungen und Herausforderungen zu stellen – Stichwort adaptive Produktion.
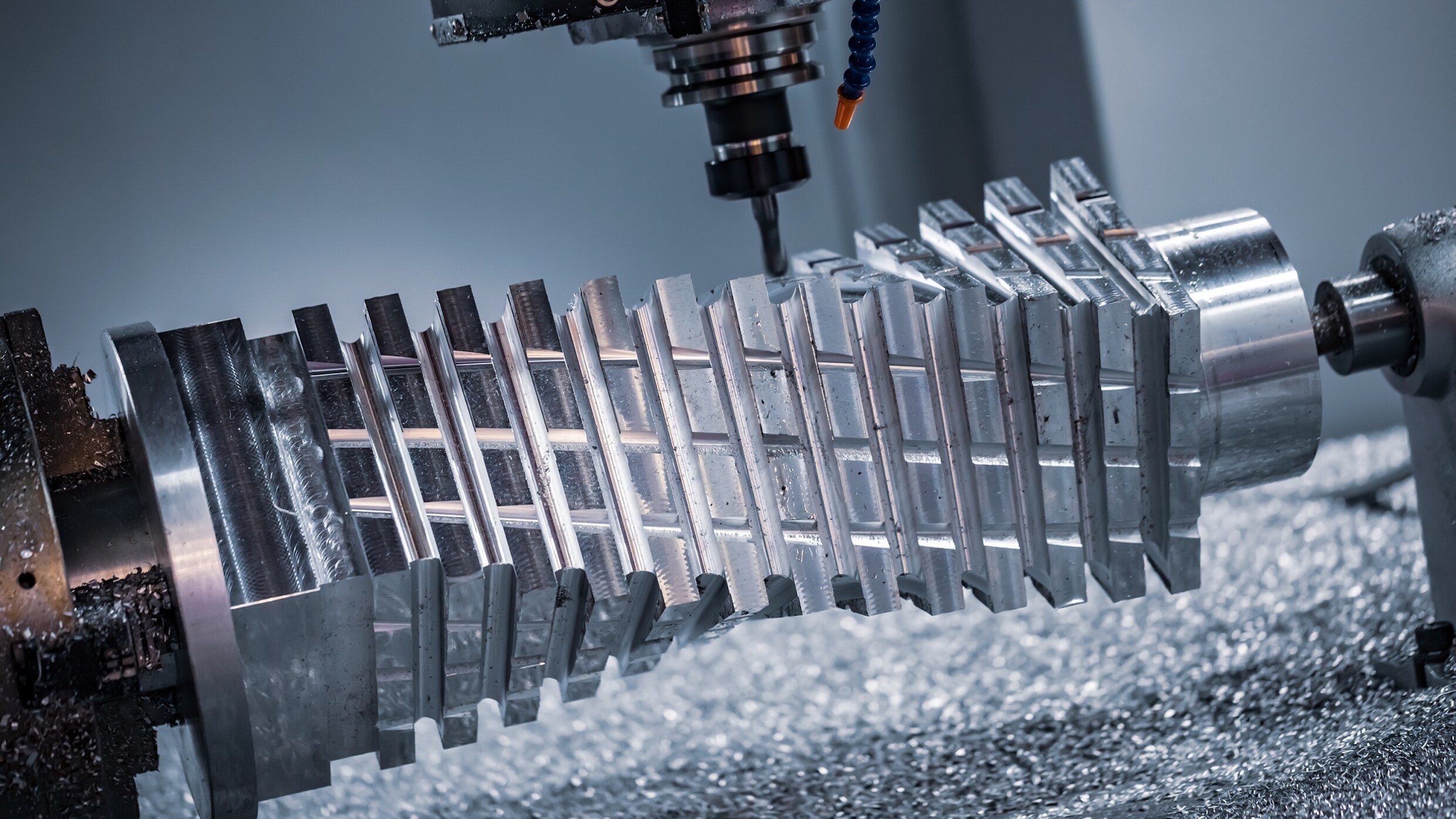
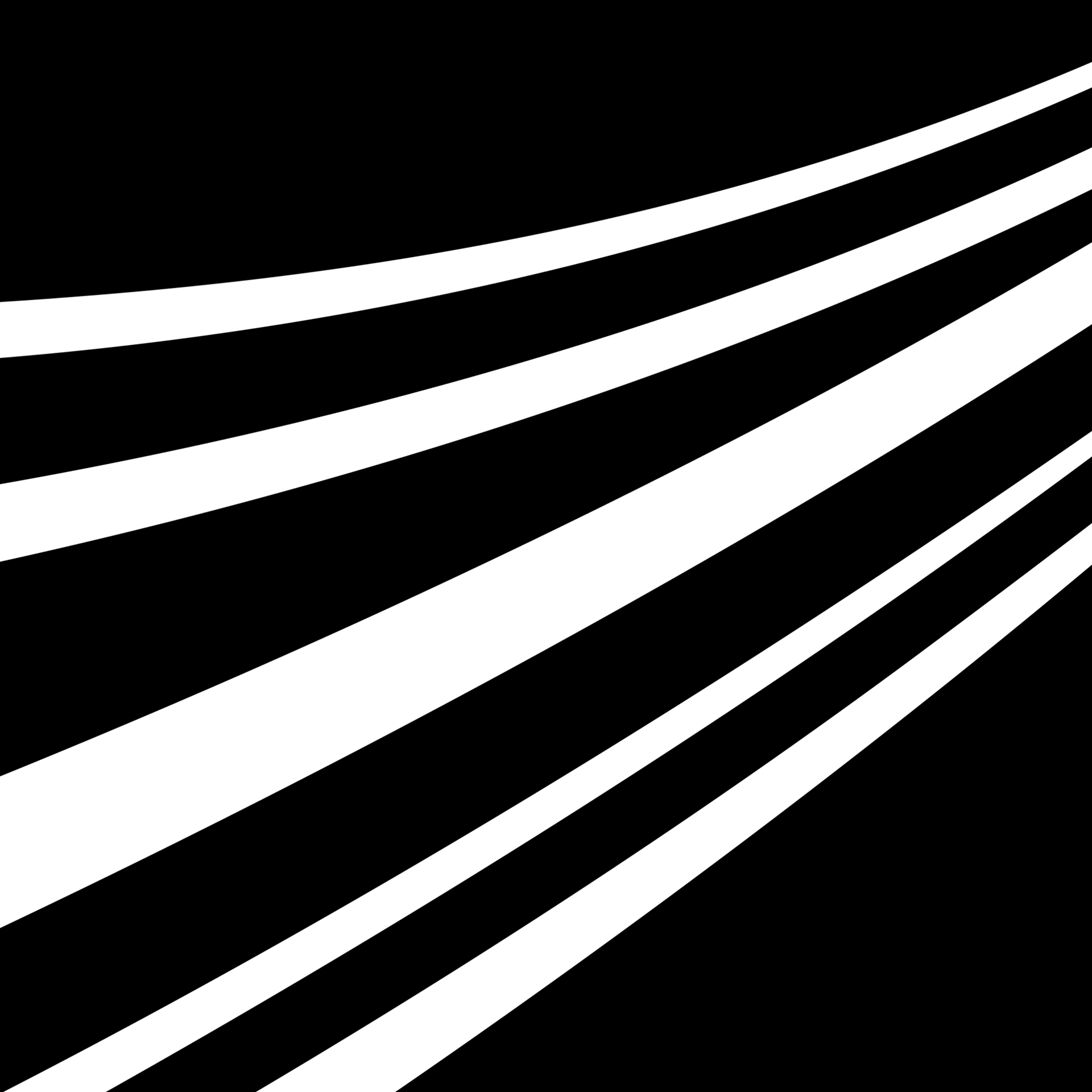
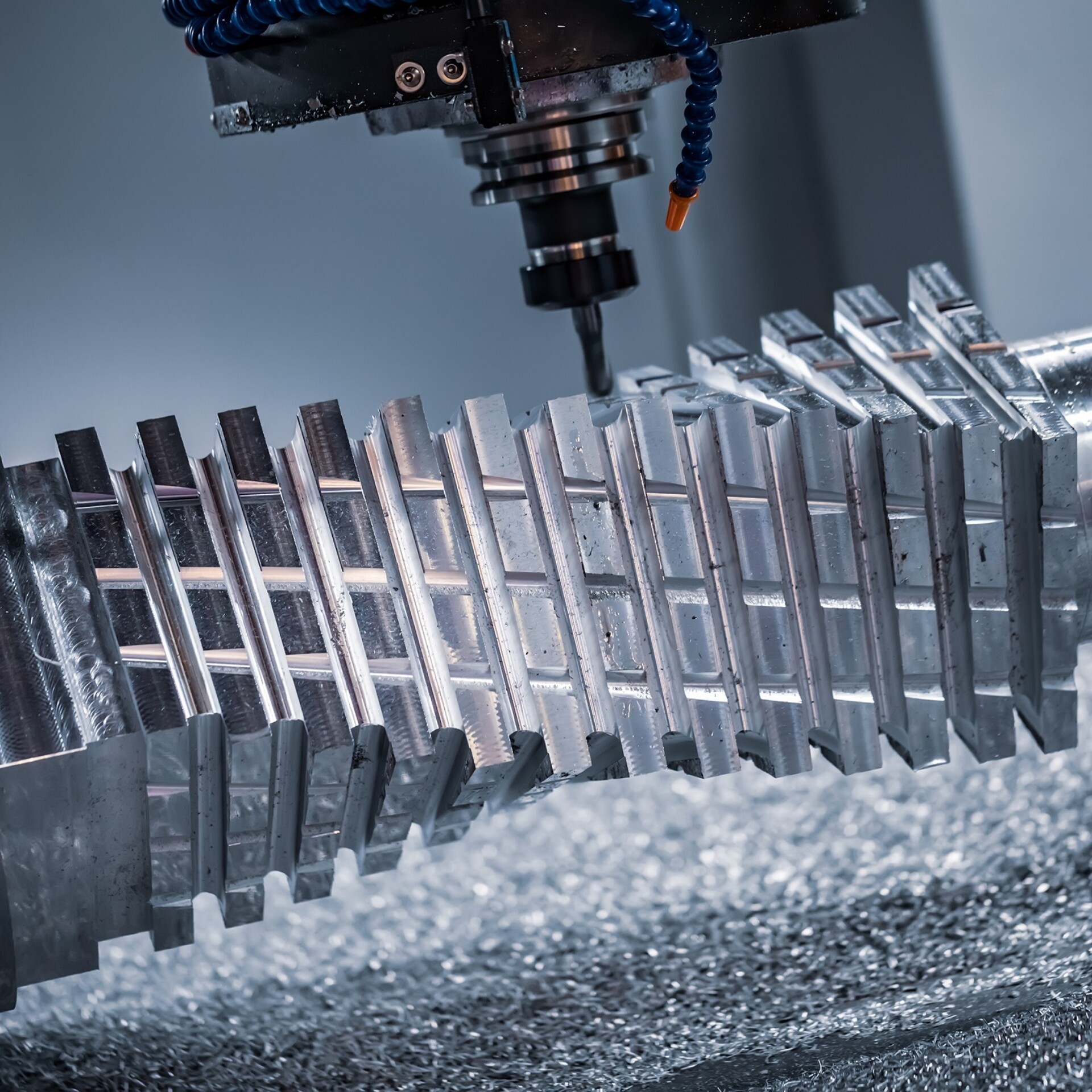
© iStock/cookelma
Mit dem Ansatz der Industrie 4.0 verändert sich die Art und Weise, wie wir produzieren, bereits stark. Damit werden die Möglichkeiten eröffnet, Produktionsprozesse durch die intelligente Vernetzung von Maschinen und Abläufen flexibler zu gestalten, zu automatisieren und zu optimieren. Bei den nächsten Weiterentwicklungen in der industriellen Produktion, geht es vor allem darum, den Menschen in den Mittelpunkt zu rücken und eine nachhaltige sowie resiliente Produktion zu ermöglichen. Die EU spricht bei dieser Evolution sogar von der Industrie 5.0[1], andere wiederum sehen den Begriff kritisch.
Jedenfalls verändern sich mit dem immer stärker beschleunigenden Innovationsdruck durch die Digitalisierung und den Fortschritten Künstlicher Intelligenz (KI) in Form Maschinellen Lernens (ML) auch die Herausforderungen in der Produktion.
ChatGPT & Co. als game changer?
Künstliche tiefe neuronale Netze sind heute bereits in der Lage, komplexe Probleme zu lösen. Beispielsweise werden Large Language Models (LLMs) wie ChatGPT bereits zur Unterstützung des Menschen eingesetzt, wobei dieser jedoch die Ergebnisse immer noch als verantwortliche Person überwachen muss. So kann hiermit bereits in ersten Ansätzen die Programmierung einer SPS (Speicherprogrammierbare Steuerung) durch Generierung von Programmcode vereinfacht werden oder auch als Schnittstelle zum Produktionssystem zur vereinfachten Analyse dienen. Um solche ML-Verfahren in sicherheitskritischen Bereichen der Produktion einsetzen zu können, müssen jedoch weitere Maßnahmen getroffen werden[2].
Um eine höhere Effizienz und Flexibilität zu erlauben, sollen zum Beispiel physikalische Barrieren wie Gitterkäfige in der Produktionsumgebung abgebaut werden. Gleichzeitig bleibt die Gewährleistung der Arbeitssicherheit, trotz der wegfallenden physikalischen Sicherheitsmaßnahmen, entscheidend. Auch hier kann Maschinelles Lernen unterstützen, beispielsweise durch die kamerabasierte Erkennung von Personen in der Nähe gefährlicher Bereiche, etwa einem Roboterarm in Aktion. Entscheidend dabei ist, dass eine solche Erkennung auch ausreichend verlässlich und aus Safety-Sicht akzeptabel ist. Hier ist es hilfreich, die Umgebungsanforderungen ausdrücklich zu berücksichtigen, die sogenannte Operational Design Domain.

© Fraunhofer IKS
Abbildung 1 Schematische Darstellung der Absicherung einer Roboterarms mittels KI-gestützter Personenerkennung in einer definierten ODD, die zur sicheren Abschaltung („OFF“) führt.
Mit solchen Einschränkungen und weiteren Maßnahmen zur Absicherung der ML-Komponenten, wie ML-Engineering, Monitoring oder Cross-Validierung, können die Potenziale von an sich unsicherem ML auch in Produktionsumgebungen genutzt werden. Werden mobile autonome Roboter in Kooperation mit Menschen eingesetzt, sind zudem umfassendere und adaptive Sicherheitskonzepte notwendig, wie wir sie am Fraunhofer-Institut für Kognitive Systeme IKS erforschen. Diese Konzepte stellen eine hohe Auslastung bei gleichzeitiger Gewährleistung der Safety sicher.
Digitale Zwillinge als virtuelle Versuchskaninchen
Weitere Möglichkeiten bietet der Einsatz sogenannter Digitaler Zwillinge, der eine digitale Repräsentation der realen Elemente darstellt. Hier hat sich mit der Verwaltungsschale (engl. Asset Administration Shell, AAS) ein standardisiertes Konzept etabliert, welches eine solche Darstellung ermöglicht. Zahlreiche Hersteller bieten bereits AAS für ihre Produkte an, sodass eine einfache Nutzung der Daten möglich ist.
Neben den statischen Informationen zu einer Komponente können auch zur Betriebszeit anfallende, sogenannte dynamische Daten genutzt werden, um ein möglichst umfassendes digitales Bild zu erhalten. Solche Informationen in Form eines AAS-Laufzeitmodells sind die Grundlage für flexible Anpassungen wie sie beispielsweise für Losgröße-1-Probleme – also der Fertigung individueller Produkte – notwendig sind.
Ohne flexible und adaptive Architekturen
geht es nicht
Für solche hochdynamischen Systeme müssen auch die zugrunde liegenden Architekturen flexibler und adaptiver werden. In der Produktionstechnik ist somit zu beobachten, wie die Standard Information Technology (IT) immer in die Operation Technology (OT) übergeht, also die produktionsnahe Steuerung aller operativen Abläufe.
Ein Beispiel hierfür ist die Entkopplung physikalischer Abhängigkeiten mittels IT-Lösungen. Sogenannte Virtual PLCs (Programmable Logic Controller), also virtualisierte Steuerungen, erlauben es prinzipiell, Steuerungscode verteilt und irgendwo entfernt in einem Rechenzentrum auszuführen, sodass man diese Steuerungen wie einen Service nach Bedarf und Auslastung der Produktion buchen kann. Virtualisierte Software-Komponenten mittels Container-Lösungen wie Docker, die auf dem PC für Entwickler üblich sind, halten auch zunehmend im OT-Bereich Einzug. Sie erlauben flexiblen Austausch und Laden von Software.
Unter anderem aufgrund der langen Lebenszyklen von Systemen im Produktionsbereich, entstehen so heterogene Landschaften, die technologische Einzellösungen verlangen. Hierbei ist vor allem die Integration neuer Technologien wie KI in bestehende Produktionssysteme und die Verbindung neuer und alter Technologien eine große Herausforderung.
Daher unterstützt das Fraunhofer IKS Industriepartner dabei, mit adaptiven Ansätzen und dem Einsatz neuer Software-Architekturen flexibler und effizienter zu werden. Zum Beispiel erlaubt das vom Fraunhofer IKS entwickelte Framework die einfache und flexible Integration von KI durch ML-Services in bestehende Produktionssysteme[3], von der Cloud bis zur tiefen Integration in Steuerungen. Auf Basis der AAS kann damit ein Echtzeitbild des Systems als digitaler Zwilling projiziert und dazu verwendet werden, die verfügbaren oder neu hinzugefügten Rechenressourcen optimal zu nutzen.
Damit ist es möglich, auf Veränderungen adaptiv zu reagieren. Ein Beispiel ist die Veränderung von Produktvarianten, die dazu führt, dass das KI-Modell nicht mehr korrekt funktioniert und nachtrainiert werden muss. Das Framework stellt hierfür die Grundlage bereit, dass dies automatisch erkannt, das KI-Modell in der Cloud nachtrainiert und wieder an der entsprechenden Qualitätsüberwachung eingesetzt werden kann. Ein weiteres Beispiel ist die einfache Nachrüstung einer kamerabasierten Überprüfung mit einem ML-Modell, was Produktionsfehler erkennen kann und sich auch einfach anpassen lässt.

© Fraunhofer IKS
Abbildung 2 Installation einer kamera-basierten KI-Überwachung an einer Produktionslinie (links) mit Darstellung des aktuellen Zustands im Dashboard (rechts)
Hohe Anforderungen an Flexibilität und Resilienz sind so kosteneffizient zu realisieren.
Wir unterstützen Sie gern bei der Entwicklung und Umsetzung solcher adaptiven Konzepte sowie bei der Integration von KI in der Produktion. Sprechen Sie uns an: business.development@iks.fraunhofer.de
Die Potenziale der Digitalisierung und KI für die Industrieautomatisierung sind also enorm. Allerdings müssen Unternehmen die Herausforderungen meistern. Mit den Arbeiten und Lösungen des Fraunhofer-Instituts für Kognitive Systeme IKS kommen Anwenderinnen und Anwender dahin, hohe Flexibilität, Resilienz und die Unterstützung der Menschen in der Produktion ebenso zu gewährleisten wie Sicherheit im Sinne von Safety in komplexen Szenarien.
[1] https://research-and-innovation.ec.europa.eu/research-area/industrial-research-and-innovation/industry-50_de?etrans=de
[2] Interview mit Mario Trapp: https://safe-intelligence.fraunhofer.de/artikel/interview-mit-mario-trapp-ki-und-software-engineering-ergaenzen-sich
[3] https://www.iks.fraunhofer.de/de/projekte/ki-integration-industrie-40.html
Die Arbeiten werden teilweise im Rahmen des Projektes »REMORA – Multi-Stage Automated Continuous Delivery for AI-based Software & Services Development in Industry 4.0« durch das Bayerische Staatsministerium für Wirtschaft, Landesentwicklung und Energie gefördert und durch die Bayern Innovativ – Bayerische Gesellschaft für Innovation und Wissenstransfer mbH unterstützt.