Nächster Artikel
Industrie 4.0
Vom Schutzzaun zur kognitiven Produktionsanlage: vier Szenarien für adaptive safety in der Industrie
Herkömmliche Schutzeinrichtungen für Menschen in der industriellen Fertigung gehen regelmäßig auf Kosten der Effizienz. Kognitive Produktionssysteme, die Ansätze von adaptive safety verfolgen, sorgen für Sicherheit und reduzieren Einschränkungen der Produktion deutlich.
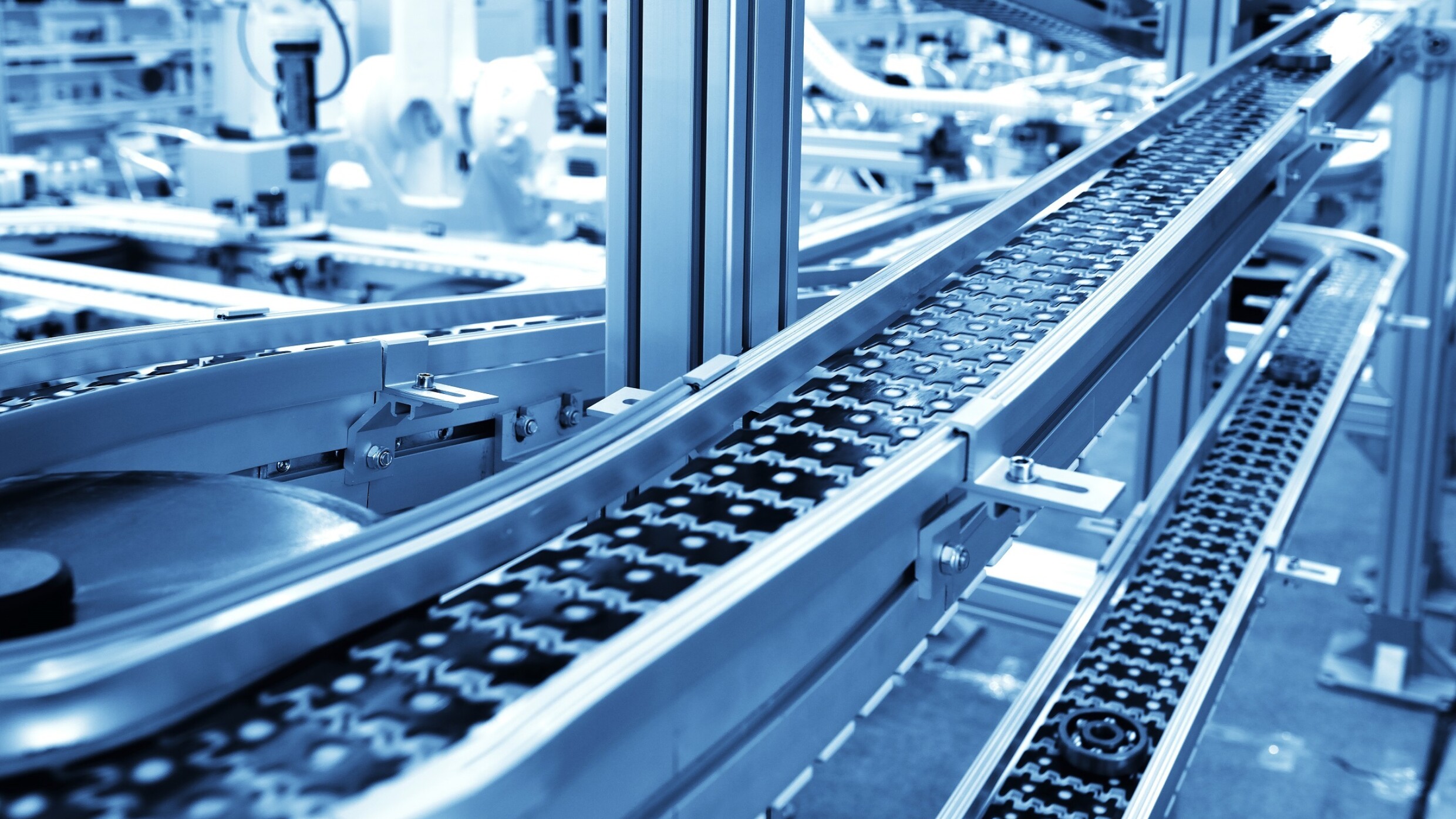
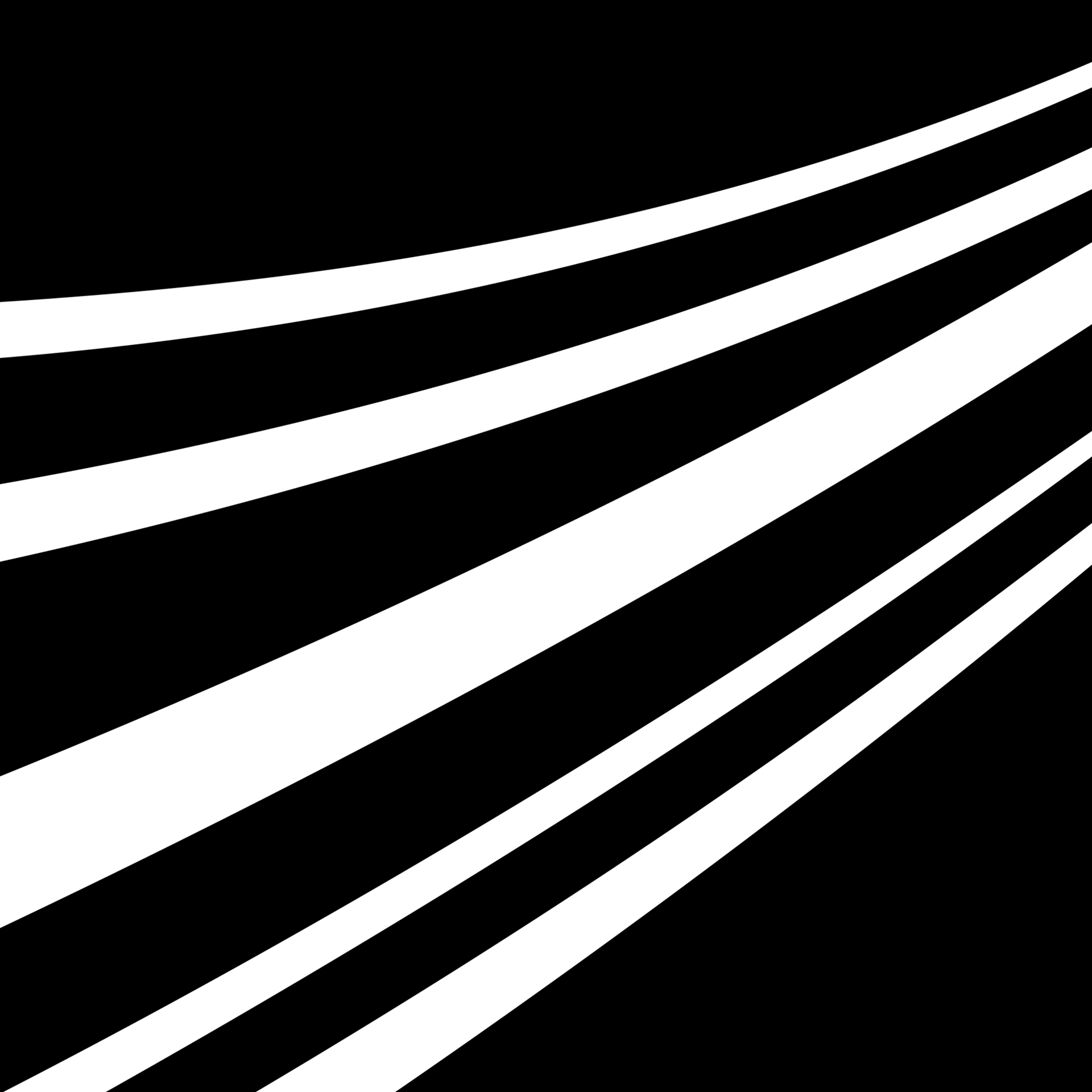
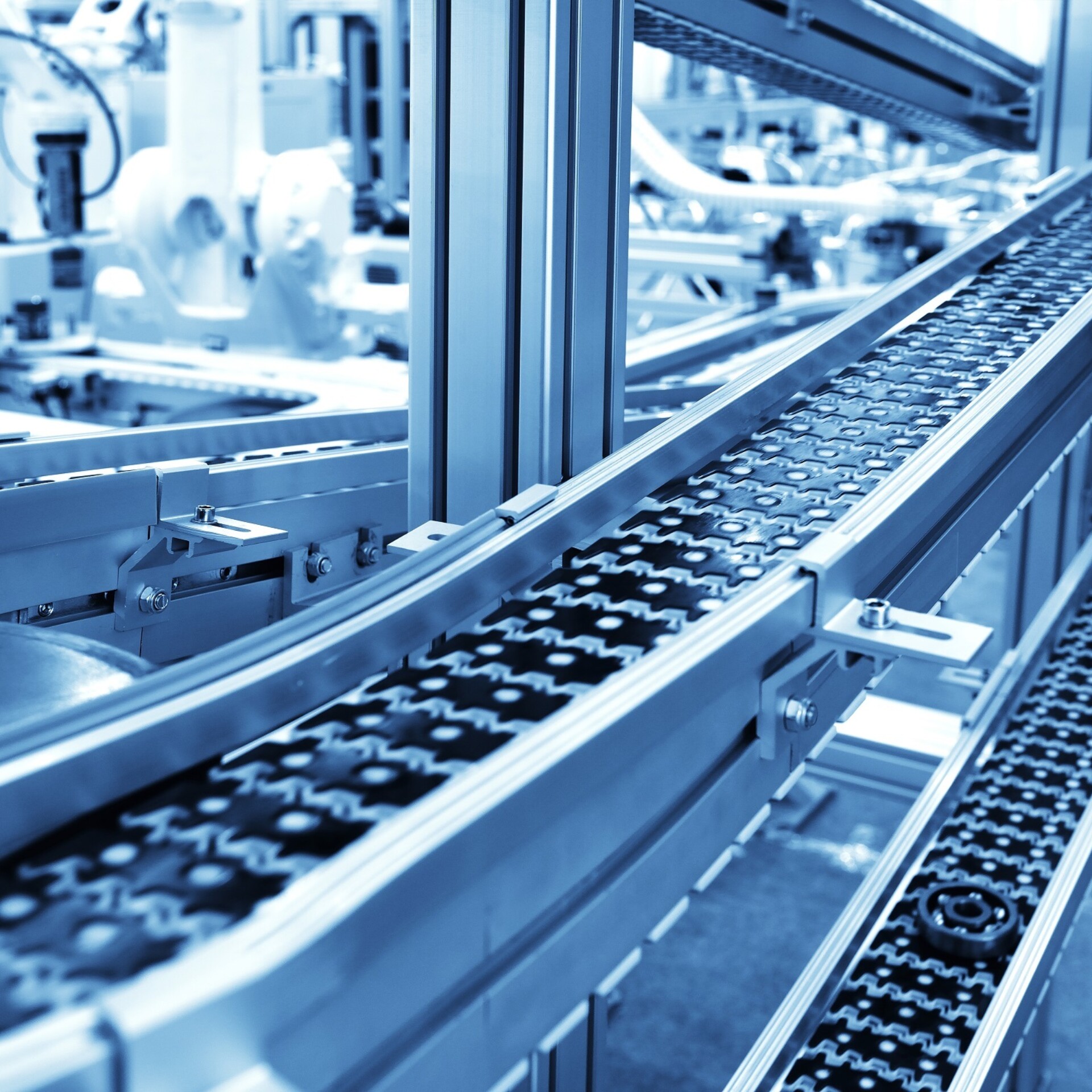
© iStock.com/zorazhuang
In Produktionshallen sind weltweit Schutzeinrichtungen wie Schutzzäune, Schutztüren oder Lichtzäune ein bewährtes Mittel, um Menschen vor den Gefahren sich bewegender Maschinen zu schützen. In Umgebungen, wo Menschen und Maschinen eher selten zusammentreffen, mag das ein probates und kostengünstiges Mittel sein. In Produktionsumgebungen mit viel Kontakt zwischen Mensch und Maschine führen Schutzzäune jedoch zu deutlicher Beeinträchtigung der Effizienz der Produktionsprozesse.
Adaptive safety in kognitiven Produktionssystemen liefert die Grundlage für Lösungen, die Sicherheit gewährleisten und dabei die Produktionsprozesse so gering wie möglich abbremsen. Dabei steht adaptive safety in der Industrie für Methoden und Algorithmen in Verbindung mit Sensoren und Aktoren, die Funktionen einer anpassungsfähigen Sicherheit bereitstellen. Ein Beispiel: Eine statische Safety-Funktion folgt dem Prinzip: »Wenn die Schutztür geöffnet wird, dann Anlage stoppen.« Bei einer adaptiven Safety-Funktion sieht das dagegen so aus: »Wenn die Schutztür geöffnet wird, dann unmittelbaren Bereich in den reduzierten Betrieb fahren. Alle anderen Bereiche normal betreiben.«
Wie das konkret aussieht, zeigen folgende Szenarien:
Cobot: vom eingezäunten Schwerlastroboter zum vorausdenkende Assistenten
Das Wichtigste für Hersteller von Industrierobotern war bislang die Positioniergenauigkeit des Greifers, etwa bei hohen Lasten. Das gilt aber auch im Hinblick auf die Wiederholgenauigkeit der Positionierung. Dagegen verlangen die Anwender immer mehr nach kooperierenden Systemen, in denen Menschen und Roboter miteinander agieren. Die aktuelle Generation so genannter Cobots, also kollaborierender Roboter, erkennt Hindernisse anhand von Drehmoment- oder Energieverbrauchsmessungen an ihren Achsmotoren. Wenn zum Beispiel ein Roboterarm auf ein unvorhergesehenes Hindernis stößt und somit sein Ziel nicht erreicht, versucht er es weiter, was sich an erhöhtem Kraftaufwand beziehungsweise Energieverbrauch ablesen lässt. Alternativ oder als Ergänzung lassen sich durch eine künstliche Haut, die nachträglich bei Industrierobotern angebracht wird, Berührungen mit Menschen erkennen. Zusätzlich besteht die Möglichkeit, die Arbeitsräume mit Kameras zu beobachten.
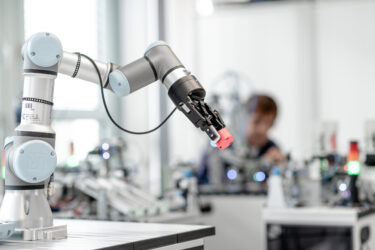
© Fraunhofer IKS/Andreas Jacob
Bei der Mensch-Roboter-Interaktion steht die Sicherheit an erster Stelle. Adaptive safety sorgt gleichzeitig dafür, dass die Beeinträchtigung der Produktion möglichst gering bleibt.
Allen liegt jedoch der Gedanke zugrunde, durch die Auswertung aktueller Informationen entweder eine Berührung mit dem Menschen zu vermeiden oder möglichst geringen Schaden zu verursachen. Künftig werden hier lernende Systeme zum Einsatz von kommen. Diese nutzen die Beobachtung des Arbeitsraums dafür, das Verhalten der Menschen zu beobachten und sich darauf vorausschauend einzustellen. Damit kann der Roboterarm seine Bewegungen trotz »dynamischer Hindernisse« so planen, dass er sich möglichst schnell, energieeffizient und unter Einhaltung höchster Safety-Anforderungen bewegen kann.
Fahrerlose Transportfahrzeuge in der Intralogistik
In Fabrik- und Lagerhallen, in denen fahrerlose Transportfahrzeuge (FTF) und gleichzeitig Menschen unterwegs sind, werden FTF deutlich ausgebremst. Das liegt daran, dass bestehende Sicherheitssysteme auf Hindernisse wie Menschen und andere FTF reagieren und deren Fortbewegung stoppen. Aktuelle, zum Teil mit Künstlicher Intelligenz (KI) optimierte Intralogistiksysteme versuchen deshalb, den Menschen als unberechenbare Komponente möglichst auszuschließen, um höchste Performance zu erreichen. Ist in Fabrik- und Lagerhallen jedoch ein Mischbetrieb von Menschen und FTF notwendig, erreichen intelligente Systeme mit Schwerpunkt adaptive safety deutlich effizientere Prozesse: Wird das Verhalten sich bewegender Objekte systematisch analysiert und vorausgesagt, kann dies zu einem intelligenten und prozessoptimierten Miteinander führen – und damit zu höherer Effizienz.
Produktion: Eingriff bei laufender Maschine
Problematisch, aber in manchen Situationen unumgänglich sind Eingriffe in Maschinen und Anlagen im laufenden Betrieb: zum Beispiel das Zuführen von Bahnmaterial wie Papier oder Textilien, aber auch das Einrichten von Maschinen. Die Maschinenrichtlinie sieht hier Maßnahmen vor wie reduzierte Geschwindigkeit oder Drehzahl sowie die garantierte Sicht des Anwenders auf zu steuernde Teile. Diese sollen die erforderliche Kontrolle des Produktionsprozesses gewährleisten. Ein gewisses Restrisiko lässt sich aber praktisch nicht ausschließen.
Noch problematischer sind Situationen, in denen ein Eingriff in die Anlagen im Produktivbetrieb notwendig ist. Das ist etwa dann der Fall, wenn ein Sensor oder eine mechanische Komponente nachjustiert und gleichzeitig die aktuelle Charge verarbeitet werden müssen. So lässt sich ein hoher Ausschuss vermeiden, zum Beispiel in der Lebensmittelindustrie. Kognitive Systeme wären hier in der Lage, auf den Eingreifenden zu reagieren. Das könnte der Fall sein, indem etwa der Bereich der Maschine auf den Menschen Rücksicht nimmt und die entsprechende Zone mittels eines sensorbasierten Überwachsungssystems bestmöglich absichert. Verlässt der Mensch den kritischen Bereich, stellt sich diese Zone wieder auf Normalbetrieb um. Adaptive safety könnte hier vor allem durch erweiterte kognitive Eigenschaften der Maschine und situationsabhängiges, adaptives Agieren erreicht werden.
In der Zukunft: die kognitive Fabrikhalle
Diese Beispiele zeigen, dass adaptive safety zu effizienteren Abläufen führen kann, und das bei hochgradiger Sicherheit. Auch häufige Probleme wie die Umgehung von Sicherheitseinrichtungen durch das Bedienpersonal ließen sich durch eine intelligente Sicherheitsarchitektur verhindern. Aber nicht nur einzelne Maschinen und Anlagen könnten von einer adaptive safety-Architektur profitieren, sondern auch die gesamte Fabrikhalle. Safety kann dann durchgängig zum Einsatz kommen, wenn alle Objekte, sowohl Maschinen als auch Personen, lokalisierbar und deren aktuelle Intention erkennbar sind. Dabei kann nicht nur die Safety erhöht werden. Ein kognitives Produktionssystem erkennt auch völlig andere Handlungen wie fahrlässiges oder mutwilliges Verhalten, wodurch Schaden an der Anlage vermieden wird. Dann wäre nicht nur dem Menschen, sondern auch der Maschine geholfen.
Sie wollen Ihre Produktion flexibel und sicher gestalten?
Anmeldung zum SAFE INTELLIGENCE Newsletter
Sie wollen immer auf dem aktuellsten Stand sein und regelmäßig Informationen zum Fraunhofer IKS erhalten? Dann melden Sie sich hier zu unserem Newsletter an: www.iks.fraunhofer.de/newsletter