Read next
Industrial Automation
Laying the Foundation for a New Manufacturing Paradigm
As production technologies continue to evolve, it can feel like companies are permanently playing catch-up. Read on to understand the current key changes in industrial automation and why it is worthwhile to embrace them.
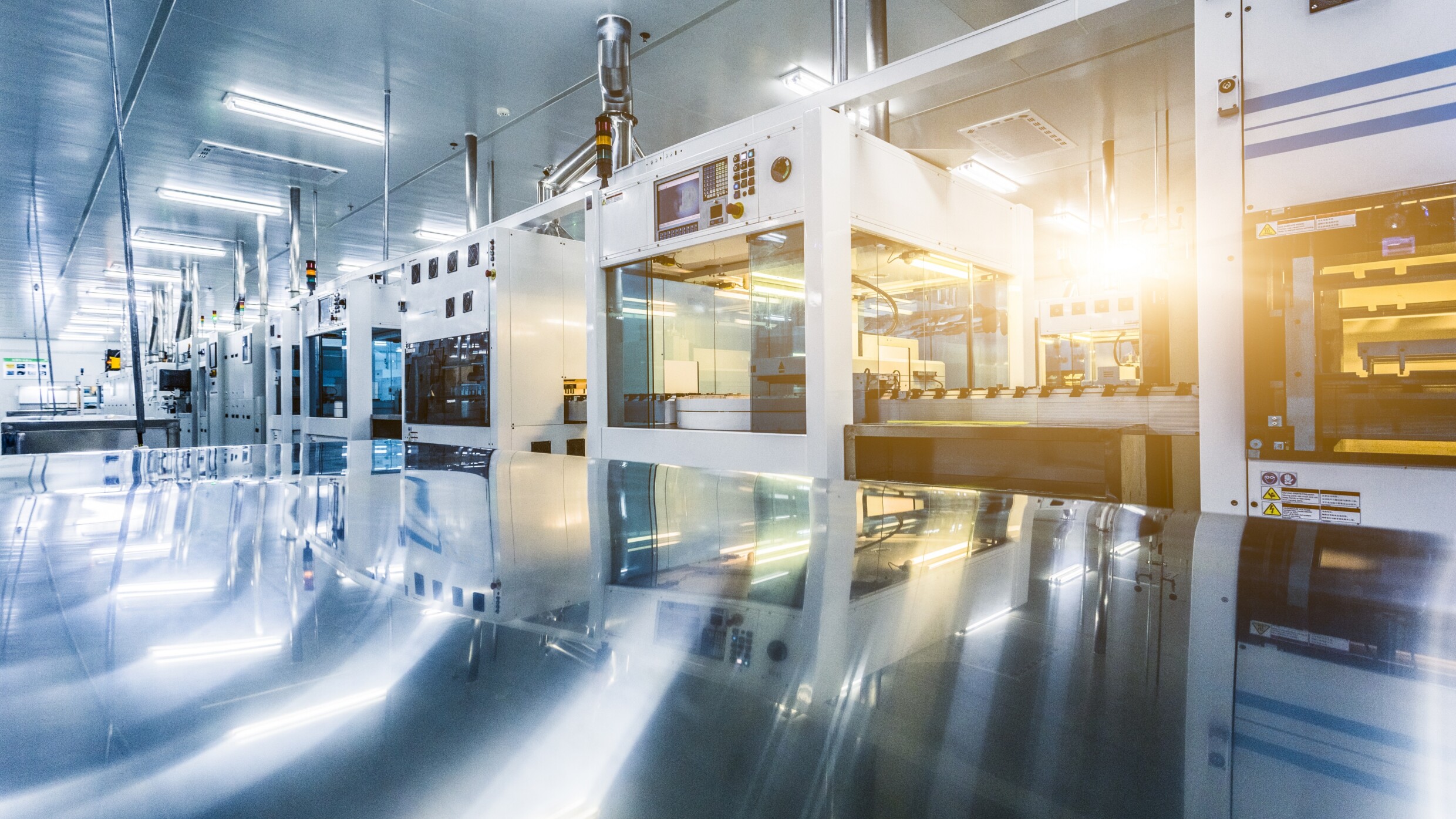
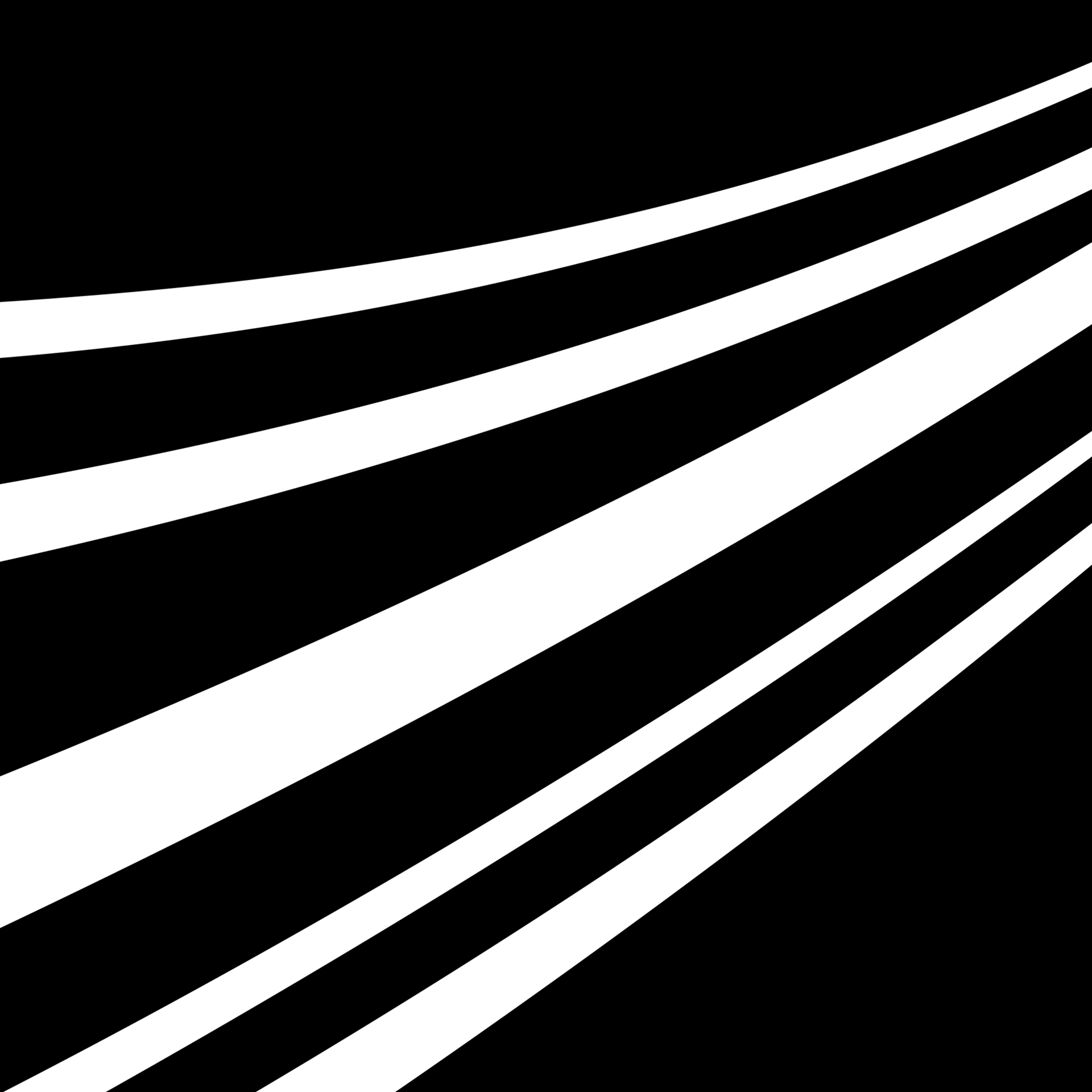
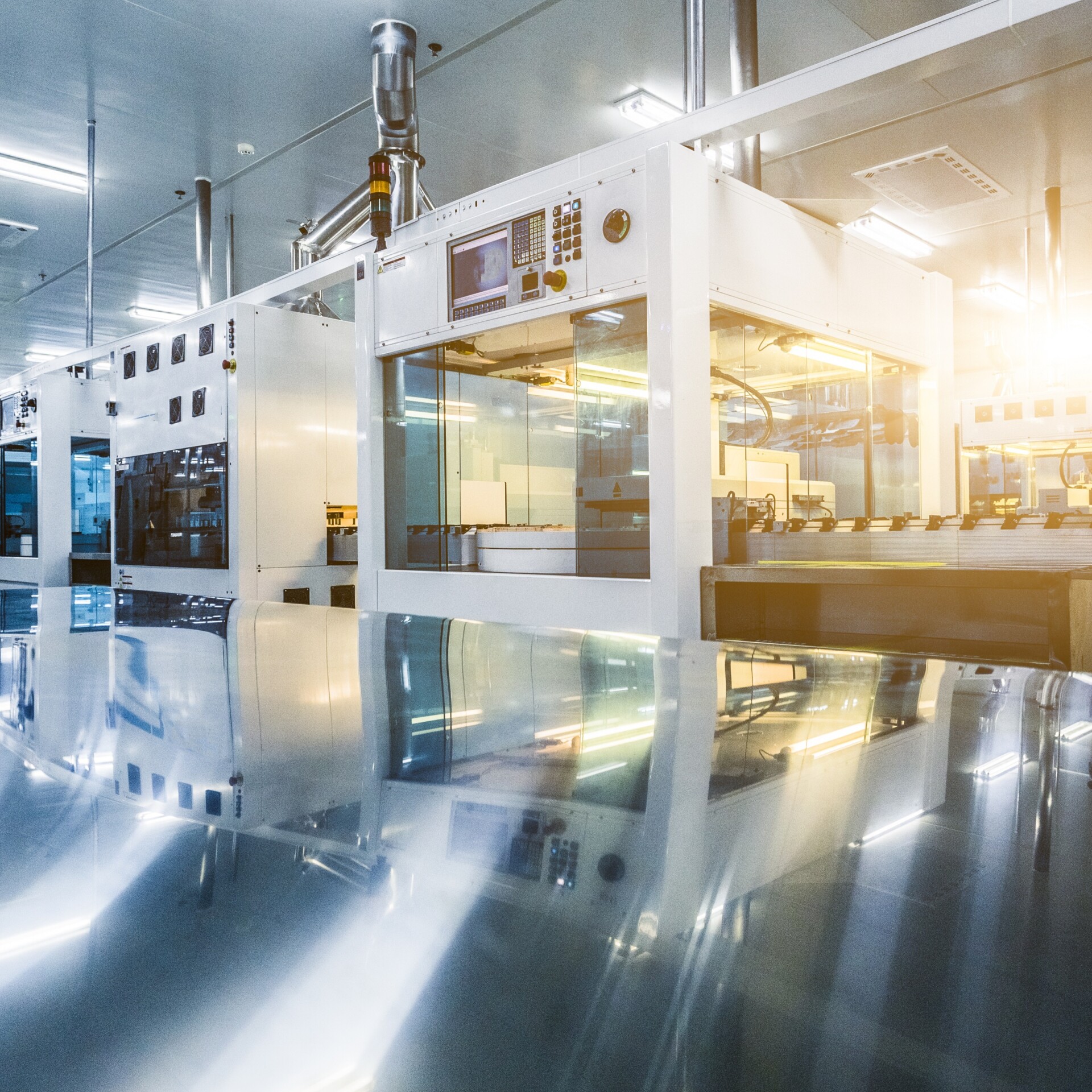
© iStock/chinaface
With the ongoing waves of modernization in production, manufacturing companies have needed to be quick on their feet, adopting new ideas to remain competitive. Until recently, the paradigm of Industry 4.0 has guided this transformation, with a focus on the digitalization and automation of the shop floor. However, companies are now beginning to step back and examine the bigger picture, increasingly considering the role of the people who work in the production line and the environment in which it operates. Looking at manufacturing through this more holistic lens can be a challenging proposition, especially since some of its principles challenge the traditional notions of production. But what does this shift in perspective look like, exactly?
Change of Focus
The backbone of Industry 4.0 is the collection and analysis of production data. By having this information at hand, it is possible to employ sophisticated techniques to optimize manufacturing and make informed decisions. The goal is to reach a smart factory state, where tools such as digital twins and artificial intelligence models connect the virtual and real worlds. This enhanced manufacturing environment, in turn, helps to improve efficiency and maximize revenue. This new shift in manufacturing, which the European Union (EU) refers to as Industry 5.0, builds upon these ideas, also considering the ethical and human aspects of manufacturing. On the one hand, it prioritizes reducing environmental impact and adopting sustainable practices. This may translate into increased shop floor flexibility, integration, and resilience. On the other hand, it recognizes the central role of humans in manufacturing processes, including human-machine collaboration scenarios and the development of new skills.
From a business perspective, examining the whole production context from this vantage point reveals additional gaps that must be addressed to improve the health of a company. This work is funded by the Bavarian Ministry for Economic Affairs, Regional Development and Energy as part of a project to support the thematic development of the Institute for Cognitive Systems. Thus, we propose to divide them into three key pillars. Understanding how to invest in these focus areas can bring concrete returns and ensure that a company is well positioned for the future.
Flexilient Automation
The first pillar to consider is that of flexilient automation, where this term refers to systems that are simultaneously flexible (i.e., can change with respect to new requirements), intelligent (e.g., integrate artificial intelligence), and resilient (i.e., are robust against failures). When thinking about flexibility, the goal is to quickly respond to changes in production, e.g., by allowing product variants to be manufactured in quick succession. Intelligence reflects the increasing usage of machine learning to solve complex tasks, such as the use of LLMs (Large Language Models) to assist in designing solutions or DNNs (Deep Neural Networks) for pattern detection. Resilience entails the adoption of strategies to keep the production line operational even when it has been impacted by unforeseeable problems, e.g., broken machinery or unexpected obstacles for robots.
Investing in flexilience can lead a company to tap into new markets and explore new business models, since it enables the manufacturing of smaller product quantities and encourages faster turnaround times. Additionally, it ensures that production levels remain high, as the production line itself adapts to work around unanticipated issues like supply-chain delays.
Reliable Human-Centered Automation
Adding to the idea of flexibility and resilience, the second pillar focuses on human-centered automation, where the mindset is to acknowledge and leverage human skills as a fundamental part of manufacturing. In practice, many production lines are not fully automated, and collecting human input is an important part of the process. The challenge then becomes how to enable humans to make decisions that are seamlessly and safely executed by machines. It is important to highlight that the objective here is to deploy machines to support humans to relieve them of boring and strenuous work, instead of replacing workers or interfering with their tasks. Automation still leaves room for unreliable behavior, so it is important to have human experts that can verify whether machines are performing as expected. This ensures that workers can be assisted in the best possible way. Another possibility for human-machine collaboration is the development of robots that can learn specific procedures from human experts and later imitate them in an automated fashion.
By combining the strengths of humans, such as the ability for complex decision making and creative problem solving, with the advantages of automation, which include scalability and efficiency, it is possible to significantly reduce costs and increase production speed. Most importantly, human involvement ensures that the quality of the products remains high while the potential waste of resources remains low.
Sustainability
Finally, the third pillar to consider is sustainability. Not only is this crucial for decreasing the environmental impact of manufacturing, which is of utmost importance, but it also streamlines the production process by decreasing the use of resources. This can be accomplished by optimizing manufacturing processes through the employment of machine learning and other artificial intelligence techniques. For instance, sustainability can be prioritized by optimizing the scheduling of machinery to minimize the overall energy consumption during production. Likewise, the placement of machines on the shop floor can be optimized to minimize intralogistics efforts, which in turn translates into further energy savings. At a higher level, supply chains can be restructured, shortening them where possible and prioritizing the local sourcing of materials. This connects with the concept of a Digital Product Passport from the EU, which is a way of tracking the entire manufacturing life cycle of a product. This data provides insights into the resources necessary for producing, recycling, and disposing of products. By leveraging this information, it becomes possible to further reduce the overall environmental impact of this product.
Thus, investing in sustainability protects the environment, boosts local economies, fosters a company’s strategic independence (e.g., by decreasing supply chain dependency), and reduces the overall production costs. Additionally, it ensures that companies comply with current manufacturing requirements.
Where to Start
The discussion above hopefully sheds light on the importance of considering this new manufacturing paradigm, but it leaves the question of which direction to invest in first open. In fact, investing in any of them can already bring benefits, so this decision should be made strategically depending on the specific needs of the company. For example, if a company aims to increase the flexibility of its automated solutions, then investing in a framework that supports these capabilities is a good starting point. Conversely, a company focusing on expanding the interaction between humans and machines highly benefits from investing in safety engineering for their manufacturing systems. Alternatively, a company can increase its sustainability by employing machine learning or other AI techniques for dedicated tasks to help optimize the use of resources. Regardless of the specific direction, Fraunhofer IKS is actively involved in a wide range of smart manufacturing topics and can draw on its expertise to create solutions tailored to the customer’s needs. Contact us to discuss your challenges and to explore how to bring cognitive systems into manufacturing.
This work is funded by the Bavarian Ministry for Economic Affairs, Regional Development and Energy as part of a project to support the thematic development of the Institute for Cognitive Systems IKS.