Read next
Automation
The Human-Centric Factory
Rather than replacing workers, modern manufacturing approaches aim to combine human expertise and automation, leading to a production setup that increases quality without sacrificing efficiency. Read on to understand how human skills and automation can be combined on the shop floor.
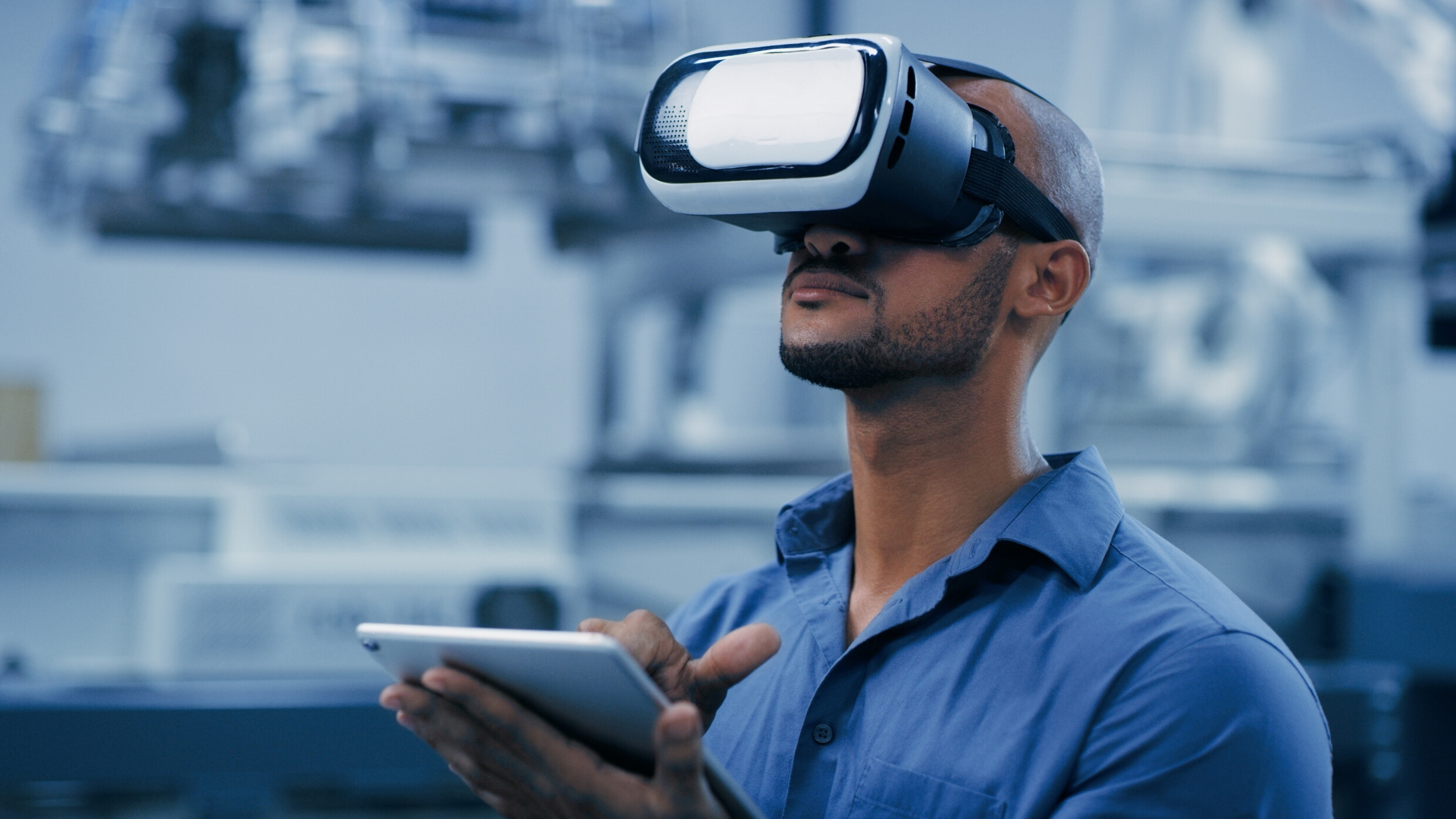
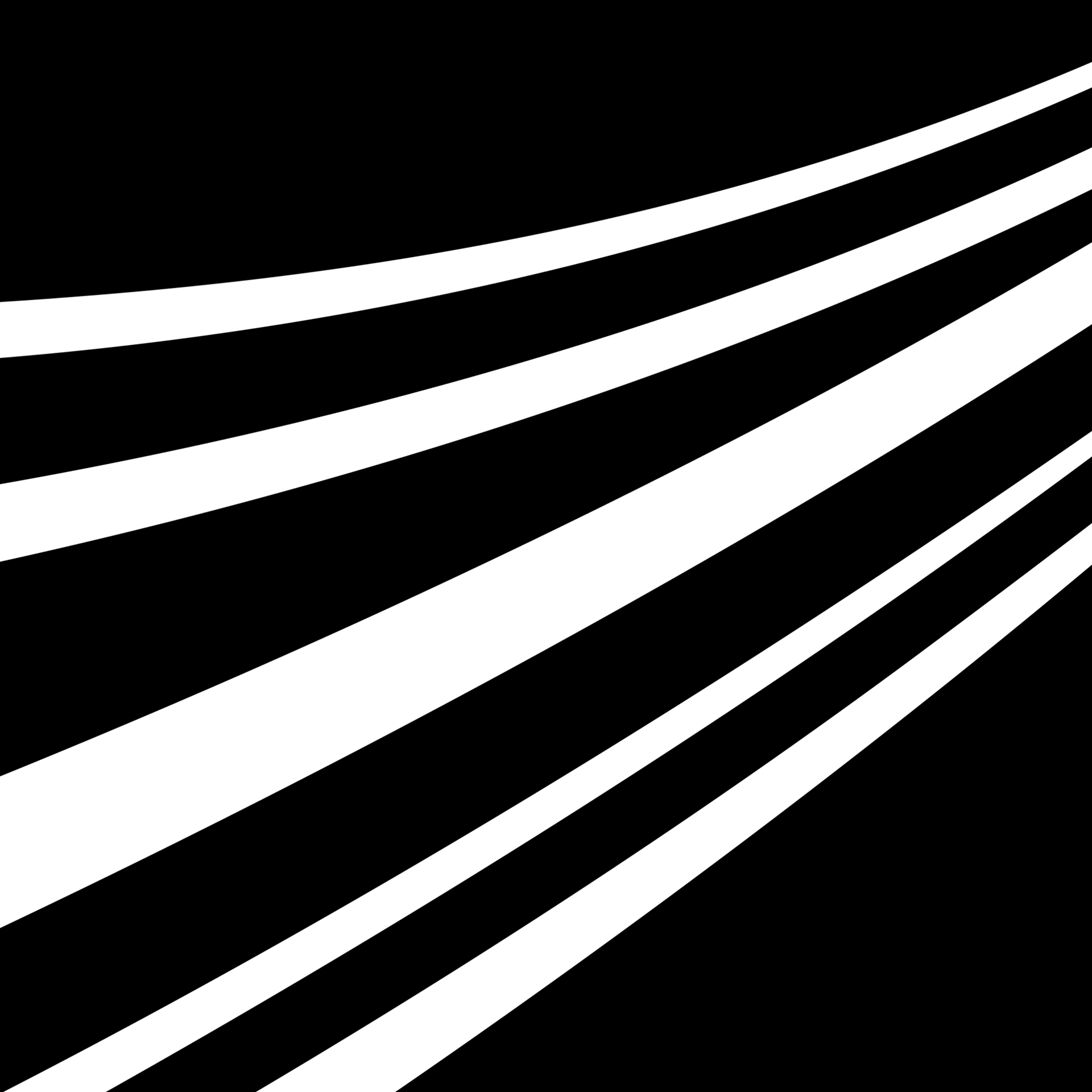
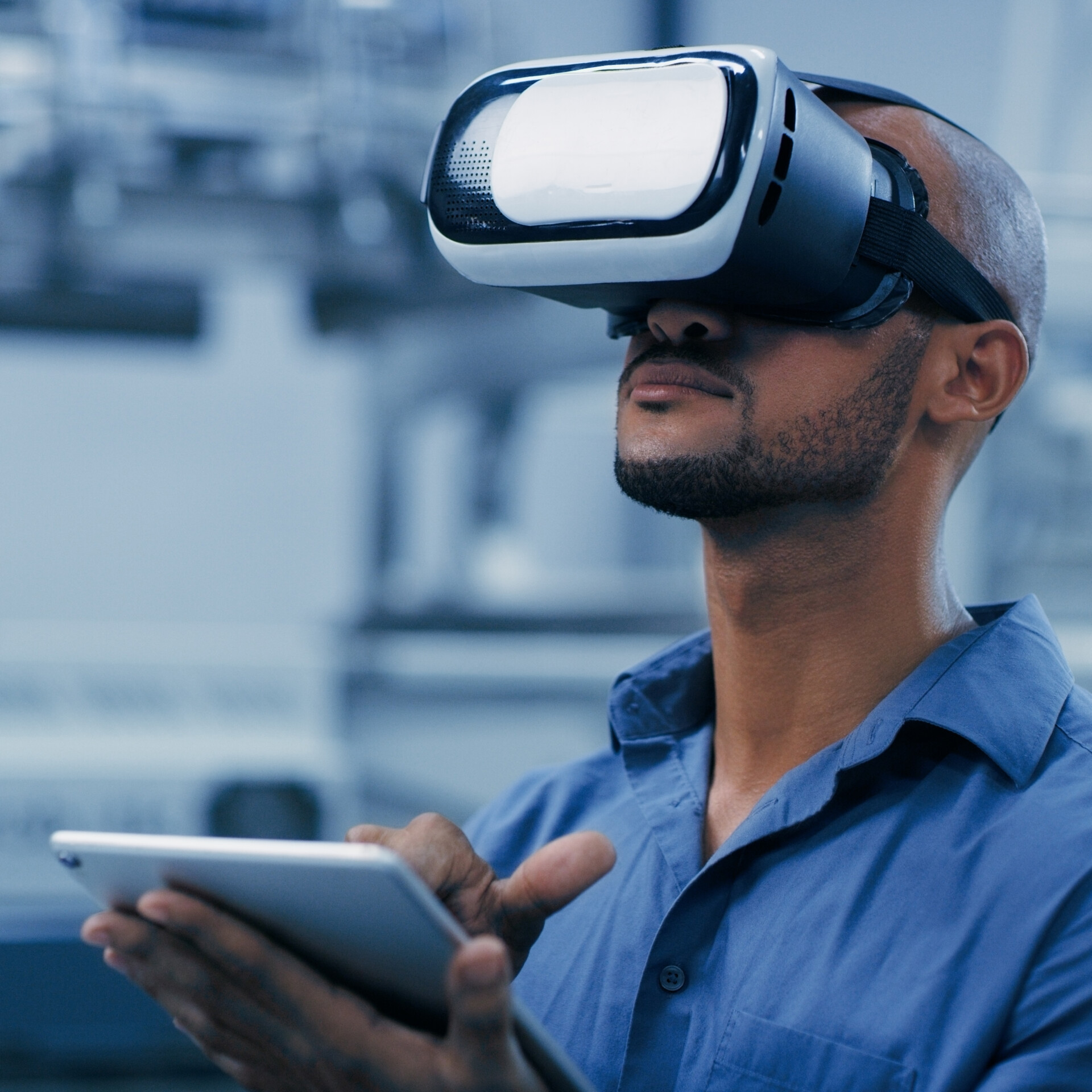
© iStock/Sean Anthony Eddy
The relationship between workers and new technology has always been complex. Ever since the industrial revolution there has been anxiety surrounding automation and the future of jobs in manufacturing. However, the human contribution to production remains indispensable in practice. For instance, when performing quality control, workers can accurately identify a wide range of potential issues, thus keeping product standards high. Likewise, tasks that involve particularly intricate or delicate assembly steps are often very challenging to automate. Finally, humans can spontaneously make decisions about the manufacturing process, which is useful when handling unexpected issues.
These examples make it clear that leveraging human skills in manufacturing is crucial, but how exactly can this be accomplished?
Collaborative Robots
One powerful way in which machines and humans can interact is by using collaborative robots. As the name suggests, these robots can directly work with people on the shop floor, e.g., transporting objects and assisting with assembly operations. This type of collaboration is ideal for hybrid production lines where certain tasks cannot be effectively automated, or where human input yields higher-quality results. In this scenario, it is very important to employ techniques that ensure the safety of workers, such as detecting potentially dangerous situations and adjusting the behavior of the robots to restore a safe environment. This includes responding appropriately to a large range of possible human actions.
Machine Maintenance
Another common scenario that can be streamlined by combining automation and human know-how is maintenance. In this case, artificial intelligence (AI) techniques can be used to predict when certain components in the production line require upkeep, and workers then use this information to perform additional checks and decide whether maintenance procedures should indeed be carried out. Although the maintenance itself must be typically performed manually, the optimal scheduling for when machines should be deactivated can also be automatically determined.
Automated Quality Control
Trained workers who have in-depth knowledge of all aspects of a product are the best at gauging the quality of the production line output. However, performing all quality control manually is expensive and, as workers become fatigued, error prone. To address this, human expertise can be leveraged as part of an automated mechanism for visual quality control. Specifically, an AI model can be trained to recognize manufacturing anomalies using human-labelled example images. This model is then deployed and independently executed, identifying common anomalies automatically. With this in place, human assistance is only required when unusual anomalies are encountered. As a result, workers are free to analyze quality trends at a higher level and more quickly identify ways to improve the production process.
Strategic Decision Making
The ability to make informed decisions from automatically collected production data is useful not only in the context of quality control, but in all manufacturing areas. For product development, for example, the data from the shop floor can be used to simulate the assembly process for new product types. This provides insight into what design elements and production parameters need further refinement. But the benefits of data-driven decision making do not stop here, and instead extend across all levels of the business, including logistics and marketing.
Augmented Reality and Generative AI Assistance
An interesting scenario that showcases the power of combining human skills and emerging technologies is the use of augmented reality and generative AI for production. The idea is to provide workers with equipment or techniques (e.g., smart glasses, AI assistants) that can guide them through complex assembly or maintenance steps. For instance, augmented reality devices can be used to display information about machines, products, and processes on the shop floor.
By considering these details, workers can catch potential issues earlier, reducing the overall number of production errors. As another example, AI assistants can be employed to automatically generate detailed layouts and manufacturing processes based on a set of product requirements. This reduces the manual planning efforts required by workers, allowing them to focus on refining specific details of the process and even on improving the original product design.
Basic Concepts and Initial Implementation
The ideas discussed thus far are clearly beneficial for manufacturing companies. However, some fundamental concepts must be implemented to put these scenarios into action. The first element is a framework that enables the collection of production data, the flexible deployment of AI techniques, and the dynamic adaptation of manufacturing processes. With this framework in place, the basic feedback loop between workers, AI, and machines is established.
The second element is the introduction of robots that can handle unexpected scenarios and adapt their behavior in the production line accordingly. By employing this technology, humans and machines can work side by side, improving production efficiency and maintaining quality standards. Finally, the third element is the use of digital human models that record how workers behave in the assembly line. This information is valuable for ensuring their safety and refining the responses of machines.
Do you have questions about human-centered production?
Please contact us to discuss your specific needs!
To implement these concepts, it is necessary to analyze the existing system and determine how these ideas can be incorporated into the current structure. This leads to the creation of an implementation strategy to guide the work. Once this has been determined, the system architecture can be modified as required to accommodate the new components. Meanwhile, prototyping and implementation for the desired use cases takes place. This is an iterative process that includes verification and validation phases.
Fraunhofer IKS can provide guidance on all aspects of this journey with our insight into the state-of-the-art. For instance, we can advise on strategic decisions, such as which manufacturing steps are the most beneficial to automate and which key technologies must be adopted as part of this transition. Likewise, we are happy to collaborate on the technical implementation of concepts, including frameworks for the adaptation of robots’ behavior and other safety-supporting features. Please contact us to discuss your specific needs.
This work was funded by the Bavarian Ministry for Economic Affairs, Regional Development and Energy as part of a project to support the thematic development of the Institute for Cognitive Systems.