Read next
Automated Guided Vehicles
How robots in warehouses operate safely and efficiently
A simulation designed by Fraunhofer IKS paves the way for robots and humans to interact safely — without reducing efficiency.
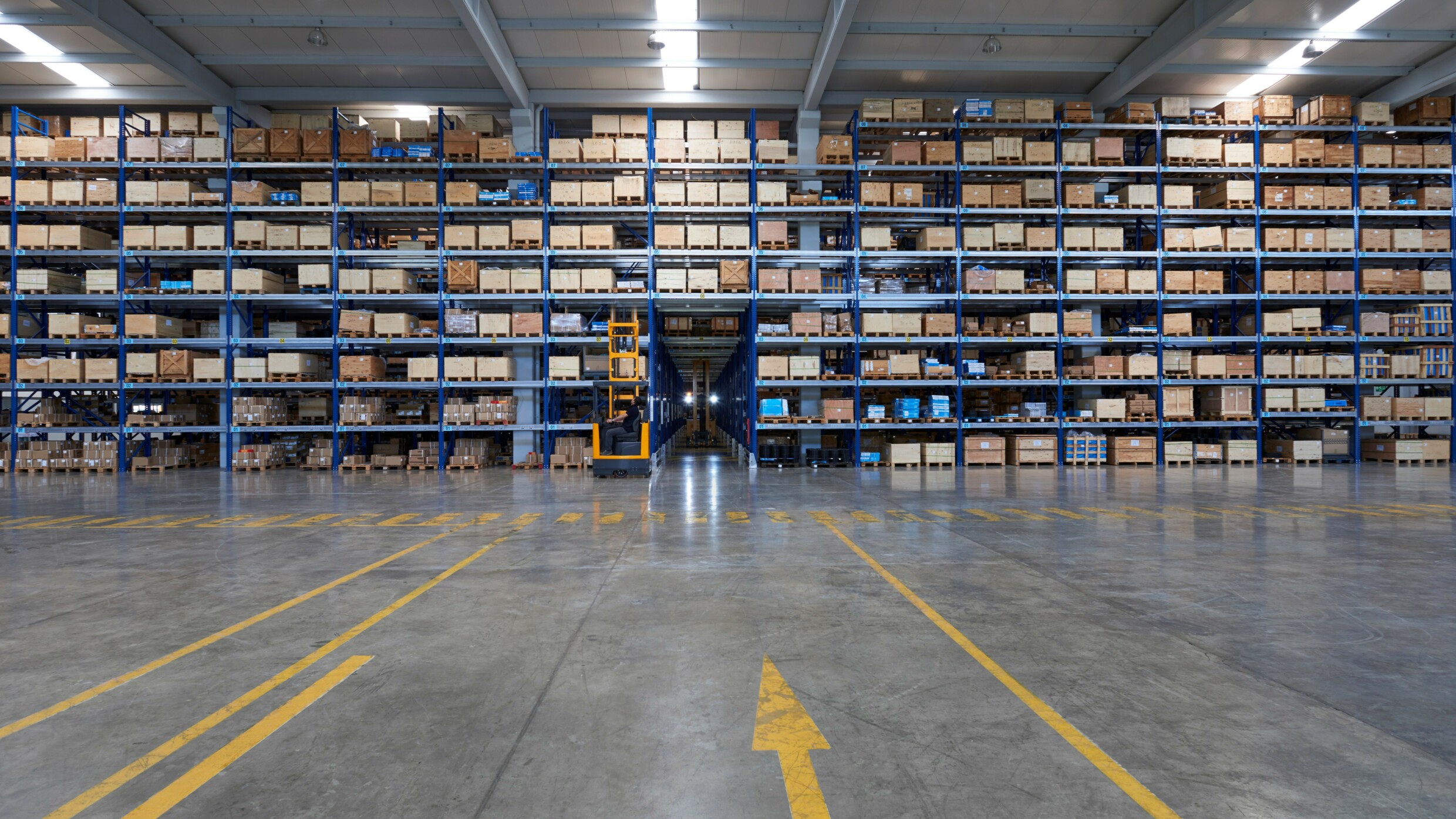
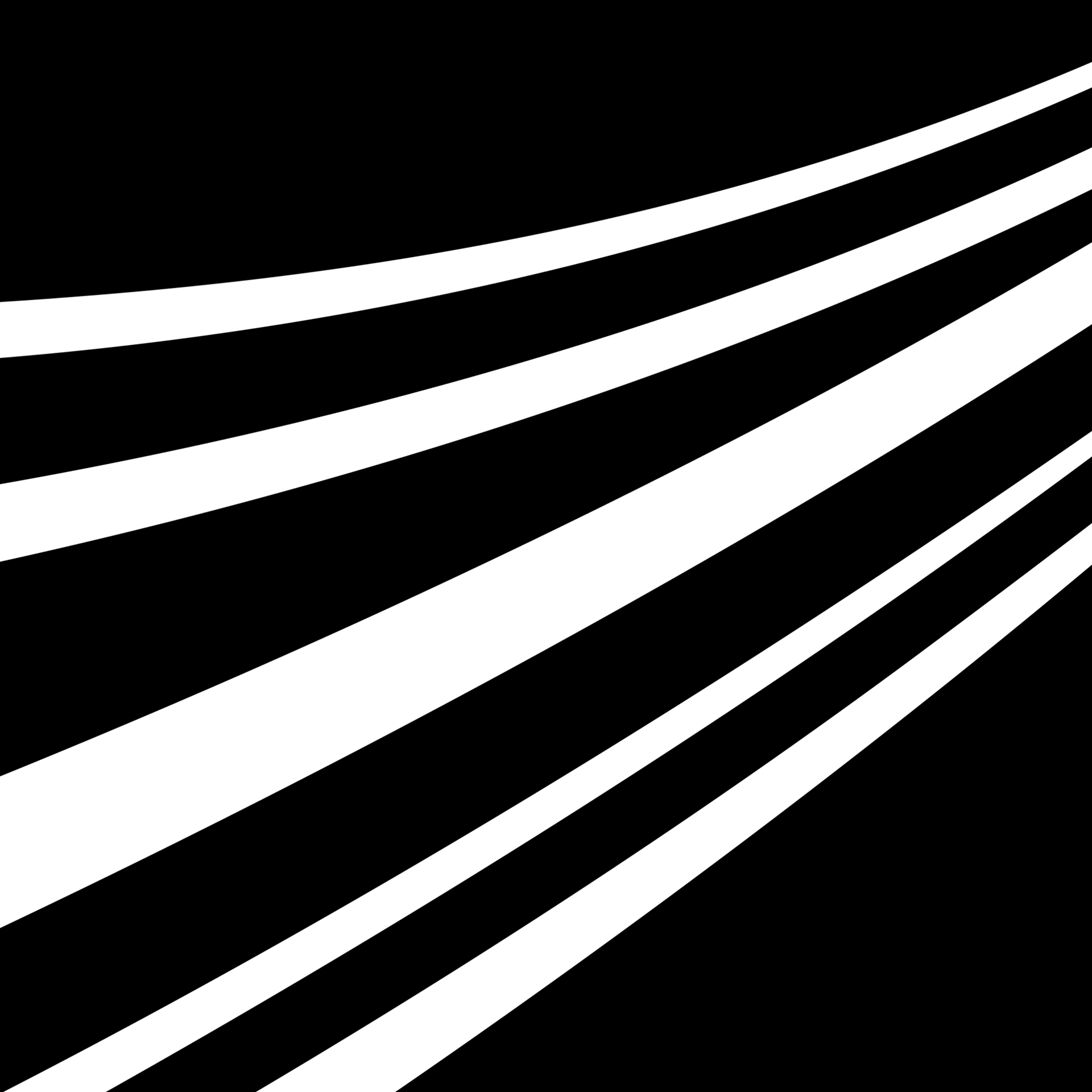
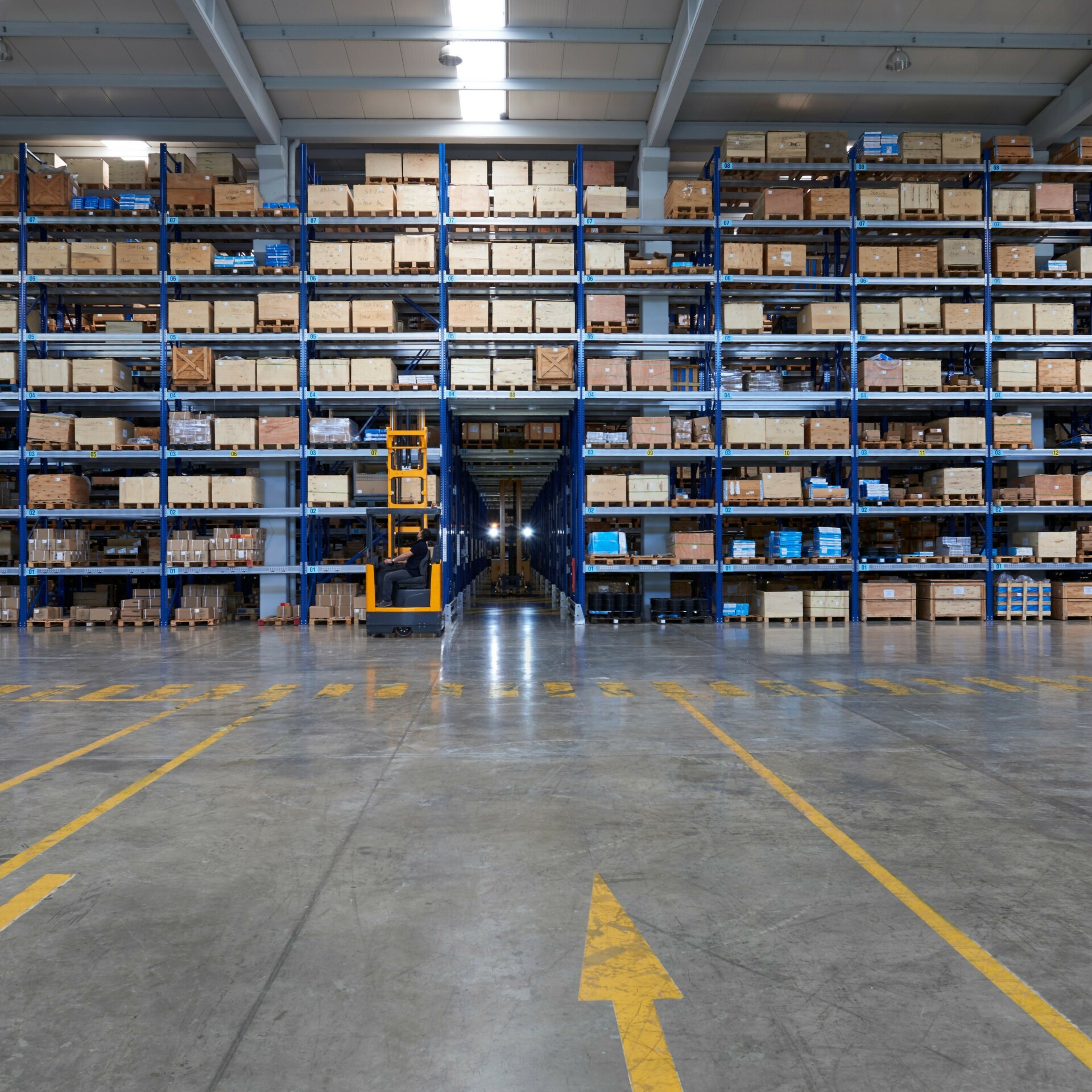
© iStock.com/stockvisual
Industrial automation has led to an increasing number of robots integrated in today’s industrial environments. However, not all tasks can be carried out by machines (yet), and it is not always feasible to segregate automated machines from human workers, e.g., by placing robots in dedicated safety cages or zones [1].
For instance, enabling personnel to be in the same area at the same time as automated guided vehicles (AGVs) allows the efficient use of human flexibility and the carrying power of machines [2]. Standards such as ISO 3691-4:2020 aim to reduce the risk of human-machine collisions, for example, by defining restrictions on the AGV’s maximum allowed speed depending on the potential hazards in the current zone of operation.
While AGVs are expected to stop if they detect a person in their path, the main burden for avoiding collisions remains with the human. In cooperation with Hitachi, we examined the impact of infrastructure sensors on the performance and safety of automated forklifts, which are AGVs for heavy loads, operating in mixed areas of a warehouse.
Conference Paper, 2021
Safe Interaction of Automated Forklifts and Humans at Blind Corners in a Warehouse with Infrastructure Sensors
Publica.fraunhofer.deBlind corners are critical
At an intersection with blind corners, humans and AGVs cannot see each other until they enter the intersection. Therefore, they need to slow down to have sufficient time to recognize intersection traffic and react if necessary. In this case, efficiency is traded for safety.
Moreover, when goods are moved, the visibility and location of blind corners may change over time. Infrastructure sensor information can be used to provide safety actions that dynamically adapt the behavior of AGVs. For example, sensors act as a kind of virtual traffic light that allows AGVs to cross intersections at higher speeds if no human is nearby and commands them to slow down or stop when needed.
However, relying on this external information introduces new hazards to a system. Different possible safety actions and strategies to activate them at runtime are conceivable. For an informed decision, their potential benefits and hazards need to be examined.
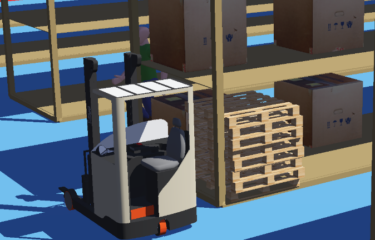
© Fraunhofer IKS
Shelves and goods can occlude the view in warehouses.
Simulating a warehouse
For this evaluation, we constructed a simulation framework for movements of AGVs in warehouses based on Webots. Webots already features a rich library of tools to simulate many different aspects of robots. For example, it provides cameras that emulate object recognition, transmitters and receivers for wireless communication as well as a supervisor API to configure and monitor simulations at runtime.
The behavior of robots and other applications can be implemented as controllers. Our simulation framework extends this with a publish/subscribe-based communication between controllers and makes it easy to set up different warehouse scenarios and evaluate safety actions.
An example layout of a warehouse has been modeled by hand and additional layouts can be quickly generated. Models of human workers and forklifts have been imported, equipped with actuators and sensors, programmed to perform simple motion tasks and are now available in the framework as ready-to-use PROTOs. This is how reusable complex objects are called in Webots.
As we did not want to dive too deep into human behavior, we programmed virtual human workers to follow scenario-based paths, and these virtual workers can be set to yield to forklifts or ignore them. Human-driven forklifts have been implemented in a similar way. Automated forklifts follow a dynamically calculated path by a central control system that coordinates the movement of automated forklifts based on information reported from the forklifts and from infrastructure sensors. Additionally, our framework implements a scenario controller that facilitates batch execution of several simulations with different configurations and scenarios.
Infrastructure sensors for safe, automated forklifts
More information about the project is available at our website.
Simulations provide the opportunity to generate early estimations of various metrics of a system without having to implement the complete system — which would likely include irrelevant elements and take more time. However, any simulation is only a model of the real world. Results obtained in the simulation are only valid within the context that the used model can provide. Nevertheless, these contexts can be shaped to suit desired goals.
When creating the simulation, we carefully examined where real-world behavior might have been simplified and how that might affect the obtained results. Using an incremental approach allowed us to test and verify our assumptions on the system’s behavior regularly. Extending and changing the context of a simulation is a great way to examine the dependability of used algorithms.
To orchestrate the movement of the AGVs, we were able to reuse a block control algorithm [3] originally implemented for an automated valet parking system with only minor adaptations. The evolution of the simulation is illustrated here.
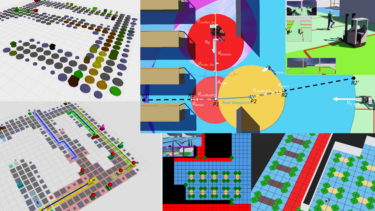
© Fraunhofer IKS
Evolution of the simulator from abstract car movements to generated warehouse layouts to simulating forklifts and humans in a warehouse.
Measuring the potential benefits and risks
Task allocation, navigation, path planning, motion planning [4] and other actions in the warehouse will influence the measured performance of AGVs. To observe the effects of each strategy in isolation, a blind corner of the warehouse was selected and scenes where a human worker and an automated forklift want to cross at similar times were examined.
The distances of the human to the corner were selected from a range that allows scenes where the human crosses before a fast moving forklift or after a slow moving forklift. This allows an estimation of the residual risk for humans in case the automated forklift is ignored and of the impact on the performance of the automated forklift. On average, automated forklifts that could benefit from infrastructure sensors could cross the intersection in about 30% less time while also avoiding all collisions.
Privacy warning: With the click on the play button an external video from www.youtube.com is loaded and started. Your data is possibly transferred and stored to third party. Do not start the video if you disagree. Find more about the youtube privacy statement under the following link: http://www.youtube.com/t/privacy_at_youtube
Looking only at the blind corner provides a limited view of the various interactions in a warehouse. The created simulation makes it possible to examine the strategies for collaborative automated forklifts in other, more general warehouse scenarios. This also allows a comparison of risk and efficiency similar to the examined blind corner scenes, with the limitation that the other listed factors also affect the results and more variations of the scenario need to be examined to avoid an unintended bias. Nevertheless, this is still feasible, as the execution and variation of scenarios is automated.
Privacy warning: With the click on the play button an external video from www.youtube.com is loaded and started. Your data is possibly transferred and stored to third party. Do not start the video if you disagree. Find more about the youtube privacy statement under the following link: http://www.youtube.com/t/privacy_at_youtube
Perhaps a more important benefit of simulating general interactions in a warehouse is the discovery of unforeseen situations and hazards. Monitors can identify critical situations in the simulation that can be flagged for manual inspection. As a result, the strategies for safe collaboration, which originally were defined with a focus on intersections, could be further improved and generalized to improve safety anywhere in the warehouse.
The constructed simulation framework will allow us to further refine safety concepts and compare them with new ideas. Moreover, the simulations can be used to explore and optimize the utility and cost of different concepts. For example, we can evaluate the effects of choosing different infrastructure sensors and integrating exclusive areas in the layout.
[1] L. Sabattini et al., “The PAN-Robots Project: Advanced Automated Guided Vehicle Systems for Industrial Logistics,” IEEE Robot. Autom. Mag., vol. 25, no. 1, pp. 55–64, Mar. 2018, doi: 10.1109/MRA.2017.2700325.
[2] R. Rey, M. Corzetto, J. A. Cobano, L. Merino, and F. Caballero, “Human-robot co-working system for warehouse automation,” in IEEE ETFA, Sep. 2019, pp. 578–585. doi: 10.1109/ETFA.2019.8869178.
[3] C. Drabek et al., “Dependable and Efficient Cloud-Based Safety-Critical Applications by Example of Automated Valet Parking,” in Intelligent Transport Systems, From Research and Development to the Market Uptake, Cham, 2021, pp. 90–109. doi: 10.1007/978-3-030-71454-3_6.
[4] M. De Ryck, M. Versteyhe, and F. Debrouwere, “Automated guided vehicle systems, state-of-the-art control algorithms and techniques,” J. Manuf. Syst., vol. 54, pp. 152–173, Jan. 2020, doi: 10.1016/j.jmsy.2019.12.002.
The research leading to these results has partially received funding from the Bavarian Ministry of Economic Affairs, Regional Development and Energy as Fraunhofer High Performance Center Secure Intelligent Systems.