Read next
Interview with Niels Syassen, SICK AG
“It makes sense to start by solving a simple problem”
Quality assurance is one of the, if not the most crucial competitive factors for industrial companies. German companies have long since recognized this and generally do not have to contend with quality issues. But that comes at a cost. Artificial intelligence is now believed to become a game changer in quality assurance. Dr. Niels Syassen, Executive Board member with responsibility for SICK AG’s Technology & Digitalization portfolio, explains how this will work.
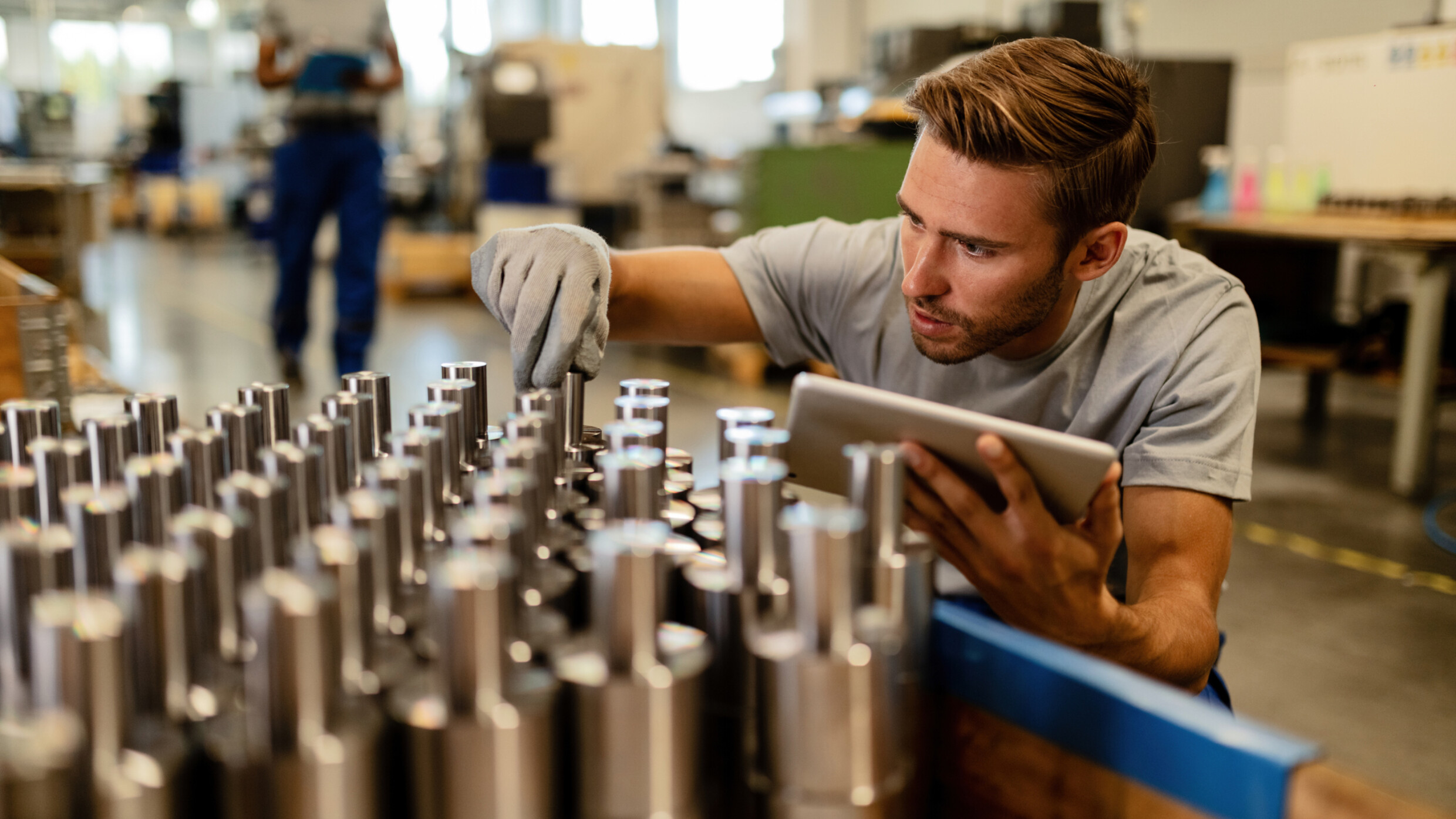
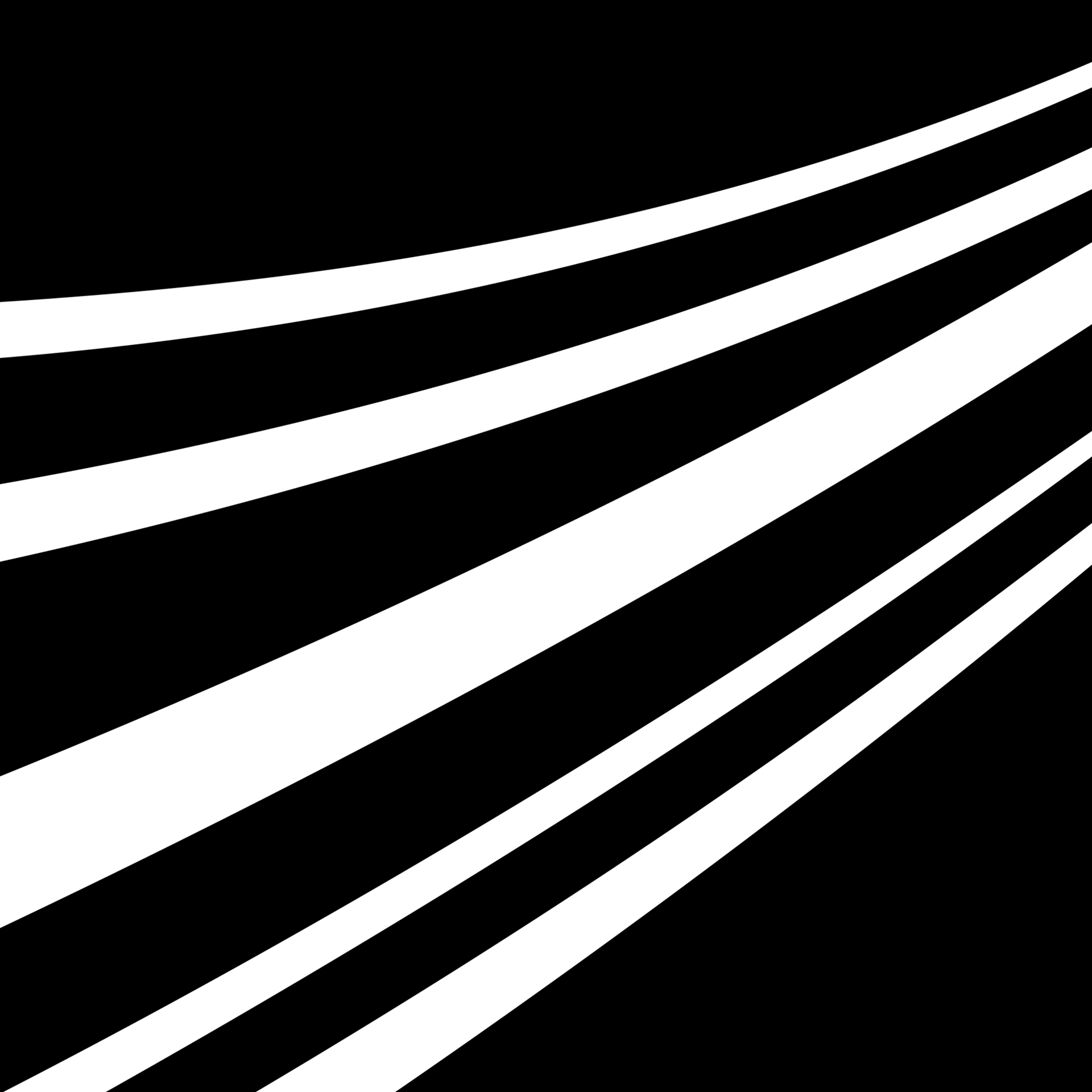
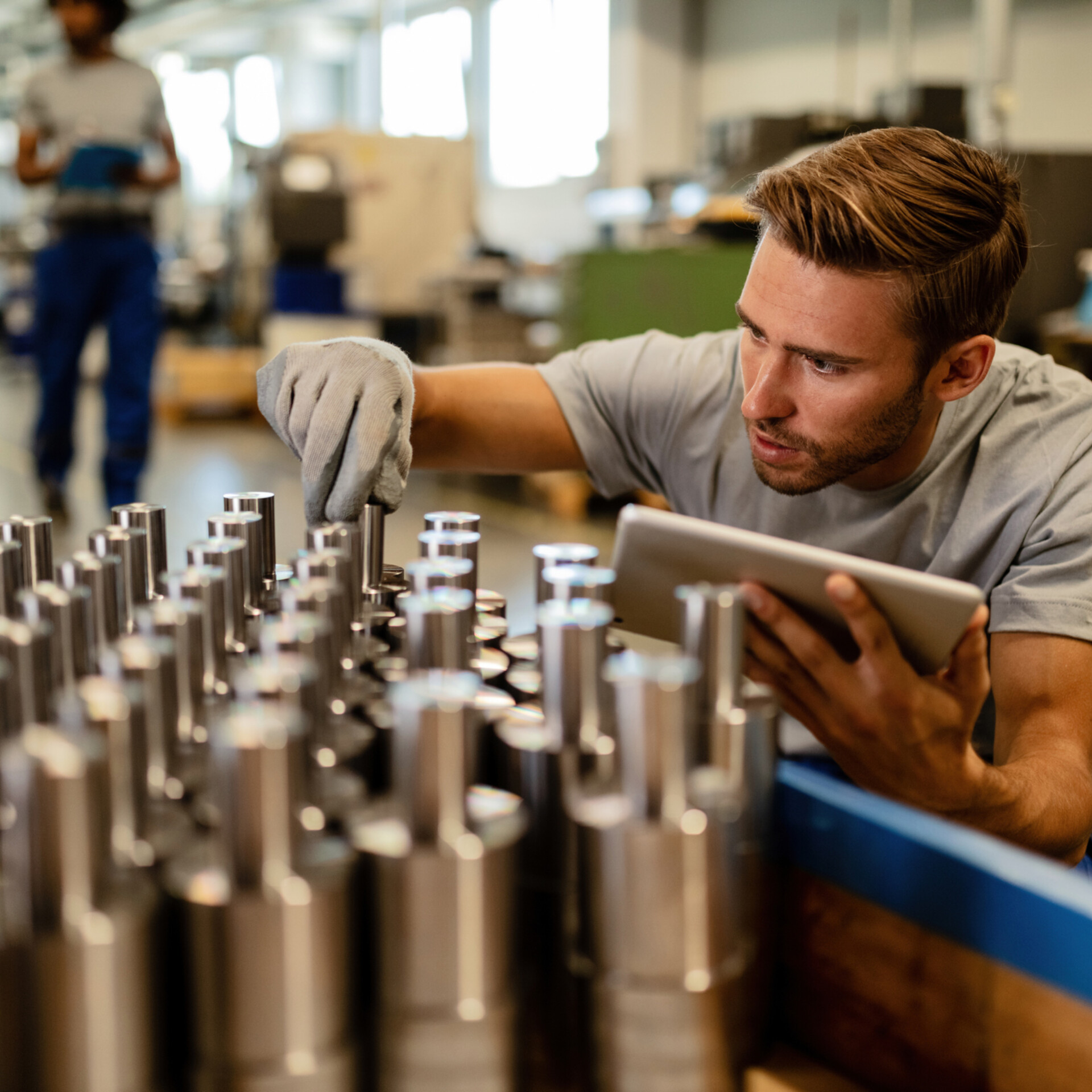
© istock/Drazen Zigic
H. T. Hengl:
Mr. Syassen, what expectations do potential users in industry have of the use of artificial intelligence (AI) in quality assurance?
Dr. Niels Syassen:
To answer that, I’d like to first explain a little what quality assurance actually is. Effective quality control aims to monitor and improve the quality of products and processes along the entire value chain. One major challenge is that many engineers are needed to develop the quality assurance systems and meet the high standards.
H. T. Hengl:
Can you give an example of this?
Dr. Niels Syassen:
SICK manufactures camera-based sensors, among other things. These cameras are integrated into the production line, and their job is to ensure quality and detect anomalies. The requirements here are very high, for example in food production. Another example is automotive manufacturing, where quality assurance deals with issues such as: Are all the screws where they should be, are specific tolerances being adhered to, for example in the engine or on the body?
H. T. Hengl:
And where does AI come into play?
Dr. Niels Syassen:
The camera sensor system is being supplemented to include AI, more precisely machine learning methods. These work well when it comes to analyzing camera images and recognizing patterns, which is crucial for quality control. So the camera and AI decide together whether a product is defective or not.
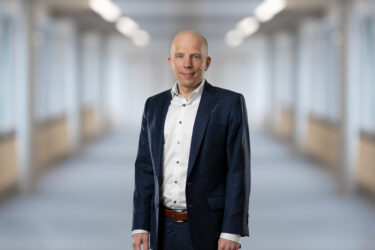
Dr. Niels Syassen: "The camera and AI decide together whether a product is defective or not."
H. T. Hengl:
How exactly can such AI-based automated solutions improve quality assurance processes?
Dr. Niels Syassen:
Combining the camera with AI makes image analysis very easy. You could call this a “plug & use solution”: You can get started right away, train the camera and AI. This significantly reduces the time and workload for quality inspections, and specifically saves on engineering costs. Because when new or different product properties come up that need to be checked, the company itself can make the necessary adjustments quickly and does not need the manufacturer to do this. The prerequisite, of course, is that the entire system is easy to use.
Dr. Niels Syassen
Niels Syassen was born in Düsseldorf in 1977. He studied physics with an emphasis on lasers, optics and semiconductors at the TU Munich as well as at Imperial College in London. He received his PhD from the Max
Planck Institute of Quantum Optics in 2008.
Since October 1, 2021, Dr. Niels Syassen has been the Executive Board member responsible for the Technology & Digitalization department at SICK AG.
He is a member of the Fraunhofer IKS advisory board.
H. T. Hengl:
What requirements does AI have to meet in quality assurance, i.e. quality inspection in the production line?
Dr. Niels Syassen:
The AI used must be very reliable, which goes hand in hand with a high detection rate in quality control. Eighty percent is not enough. It has to be 99.9 percent or more. But these last percentage points, including the decimal place, are extremely difficult to achieve. And then, as I just emphasized, the solution must be easy to use. This is the basic prerequisite if it is to be of interest to small and medium-sized enterprises.
H. T. Hengl:
What is the simplest way for manufacturing companies to use AI-based quality inspections?
Dr. Niels Syassen:
It makes sense to start by solving a simple problem and then gradually increasing the complexity or requirements. It is best to test the system to find out when and where it reaches its limits. The whole thing is then optimized in the next step. In my experience, it is better to focus on the system’s performance rather than discussing AI technology.